Referenzprojekt: Eisbär-Eis GmbH
Home / Referenzkunden / Referenzprojekte Palettierung / Eisbär
Eisbär-Eis GmbH, Plummendorf
- Anlagennummer: 10056
Vollautomatisches Verpackungszentrum mit 7 Roboterzellen zur Palettierung von Eiscremeumkartons in unterschiedlichen Abmessungen und Gewichten.
Der Kunde
Die Firma Eisbäreis produziert Speiseeisspezialitäten an zwei Standorten in Norddeutschland. Die rasant wachsende Nachfrage nach den weltweit vertriebenen Leckereien erfordert an beiden Standorten ständige Expansion durch Erweiterung der Produktionsanlagen und der für ein typisches Saisongeschäft wichtigen Tiefkühllagerkapazitäten. An dem Standort in Mecklenburg-Vorpommern wurde in der Folge der Inbetriebnahme neuer Produktionslinien und der Verdreifachung der Lagerkapazität in die Automatisierung der Verpackung investiert. Nach der dafür erforderlichen Teil-Restrukturierung der internen Warenströme wurde zur Palettierung der zu einem großen Teil in offenen Displays verpackten Produkte ein vollautomatisches End-of-the-Line-Verpackungszentrum mit mehreren Roboterzellen implementiert.
Technische Daten
- Fördergut: Umkartons, Display, Kunststoffbehälter, Becher und Paletten
- Palettentypen: EURO, INDU und CHEP
- Gewicht: bis zu 1.000 kg/Pal
- Leistung: bis zu 1.000 Pal/Tag
- Palettierung: 7 RoTeg-Linearroboter mit 4 Achsen
- Palettensicherung: Strema Doppelkopf-Drehteller-Stretcher
- Palettenbeschriftung: Bluhm-Etikettierer mit Zebra-Modul
- Antriebe: Servo-Antriebe und Frequenzgeregelte SEW-Getriebemotoren
- Steuerung: PC, Siemens S7-315DP
- Umgebungsbedingungen: 4 °C
Funktionsbeschreibung
Von insgesamt sechs Eisproduktionsanlagen und einer Anlage zur Erstellung von kundenspezifischen Sortimentsverpackungen gelangen die Produkte über zwei Sammellinien übereinanderliegend zentral in das Palettierzentrum. Mittels Barcodeidentifikation werden die Produkte erkannt und jeweils sortenrein einem der sieben Palettierzellen zugeführt und dort nach dem in der Produktdatenbank hinterlegten Packschema bis zu der gewünschten Höhe auf die vorgewählte Palettenart gestapelt. Fertige Paletten werden von einem zwischen den Palettierzellen angeordneten Zentralverfahrwagen abgeholt. Während der Vollpalettenübernahme bestückt der Verfahrwagen die Zelle gleichzeitig mit einer neuen Leerpalette. Anschließend transportiert der Verfahrwagen die Vollpaletten auf einen Übergabeplatz für die unmittelbar anschließende Stretchung und Etikettierung der Palette. Während der Übergabe der Vollpalette wird wiederum gleichzeitig der Leerpalettenspeicher im Verfahrwagen aus einem der beiden Leerpalettenmagazine mit dem für den nächsten Fahrauftrag erforderlichen Palettentyp beladen. Die fertigen Paletten werden über entsprechende Tiefkühlschleusen automatisch in eines der beiden unmittelbar angeschlossenen Verschieberegallager gefördert und dort auf Staurollenförderern bis zur Einlagerung mittels Schubmaststapler zwischengelagert.
Die beiden Leerpalettenmagazine werden über zwei Zuführungsstrecken aus einem der Tiefkühlläger automatisch mit Leerpalettenstapel versorgt.
Ausführungsdetails
Anbruchpaletten können in der „achten Zelle“ manuell bearbeitet, für eine spätere Weiterpalettierung vorbereitet und anschließend eingelagert werden. Über eine der beiden Strecken für die Leerpalettenstapelzuführung können die Anbruchpaletten zur Komplettierung dem Palettierzentrum wieder zugeführt werden. Über diese Zuführung oder über die Aufgabestation in der „achten Zelle“ gelangen auch Paletten mit evtl. benötigten Zwischenlagenstapeln in die Palettierzellen.
Steuerung
Eine SPS-Steuerung vom Typ Simatic S7-315C übernimmt die Kommunikation mit dem bauseitig vorhandenen EAP-System und den Robotern via Ethernet, sowie die konventionelle Steuerung der fördertechnischen Anlagenkomponenten und die Produktzuordnung mit Verfolgung der Warenströme. Alle Verfahr- und Drehantriebe werden mit SEW-Umrichtern vom Typ Movitrac bzw. MoviMot gesteuert.
Ein Industrie PC steuert via CAN-Bus die Roboter. Die windowsbasierte Softwareoberfläche PARO-Control bietet diverse Tools wie z.B. den bedienerfreundlichen Lagenbildgenerator zur komfortablen Erzeugung und Verwaltung der auf der Anlage benutzten Packmuster.
Zur allgemeinen Handbedienung der Anlage steht ein mobiles Operatorpanel bereit, welches im Einsatzfall durch Einstecken an einen Punkt im Sichtbereich der Anlage genutzt werden kann.
Mittels Fernwartungsanschluss kann der Kunde bei einer evtl. Störungsbeseitigung unterstützt oder Softwaremodifikationen aufgrund von Kundenwünschen kostengünstig durchgeführt werden.
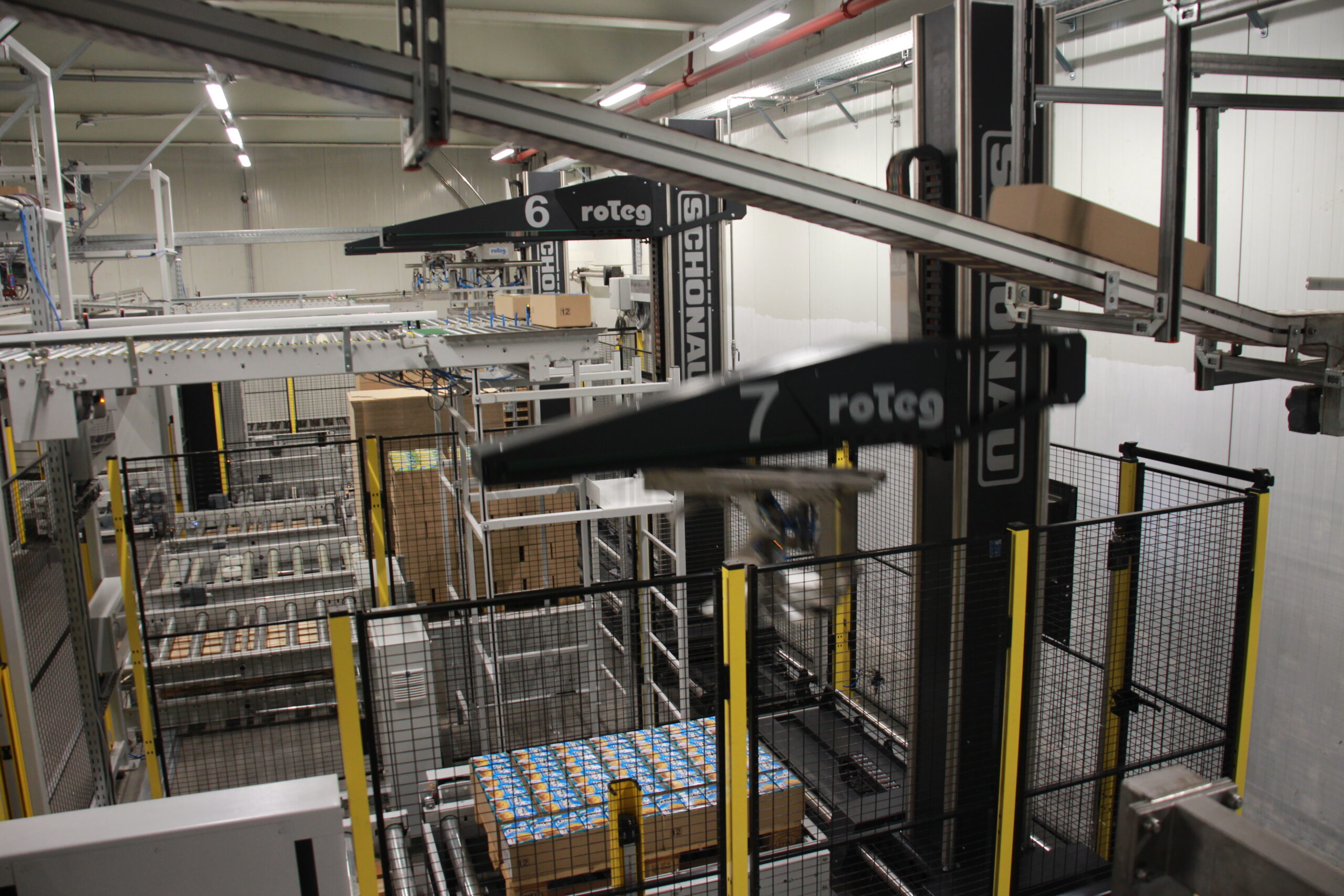
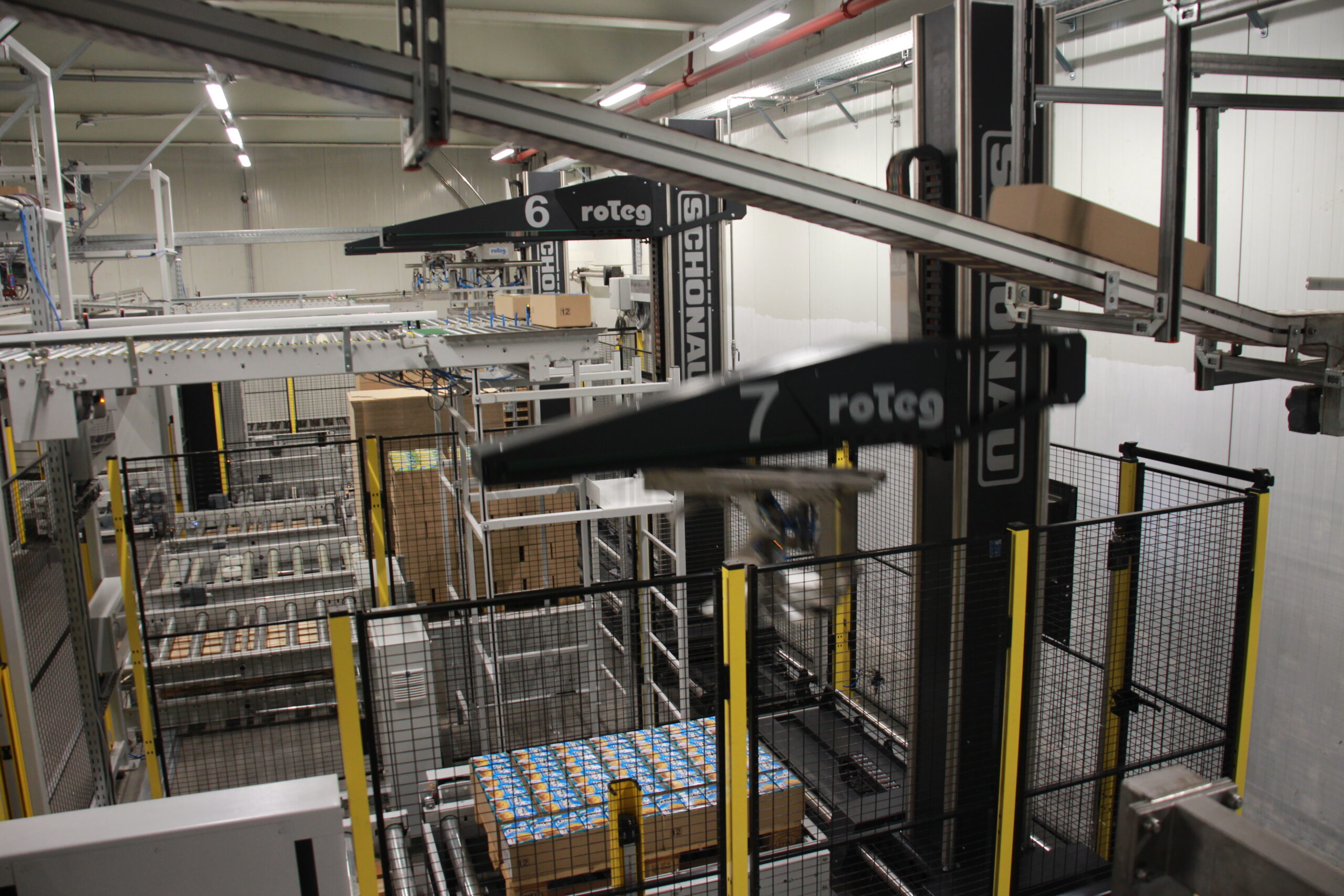
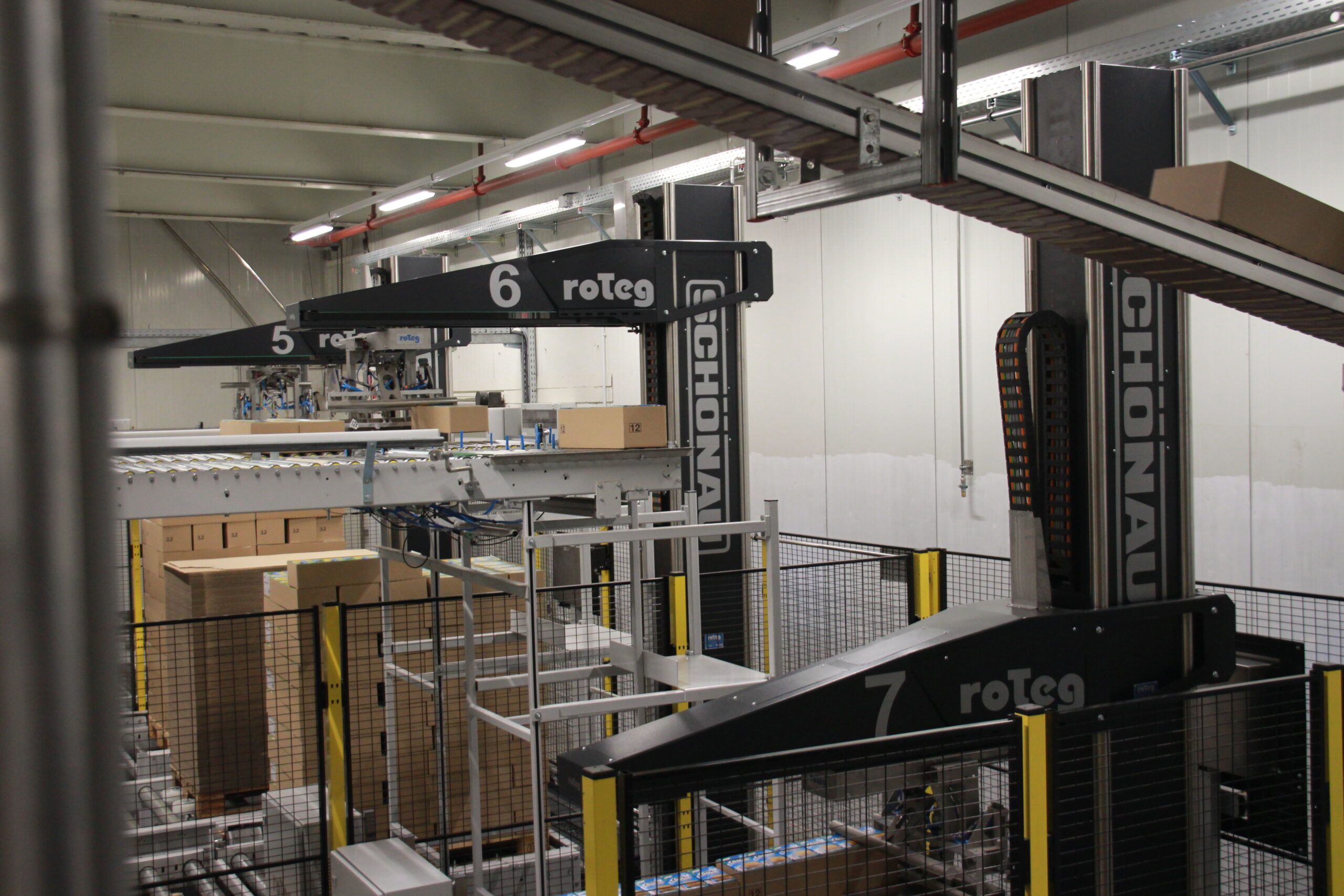
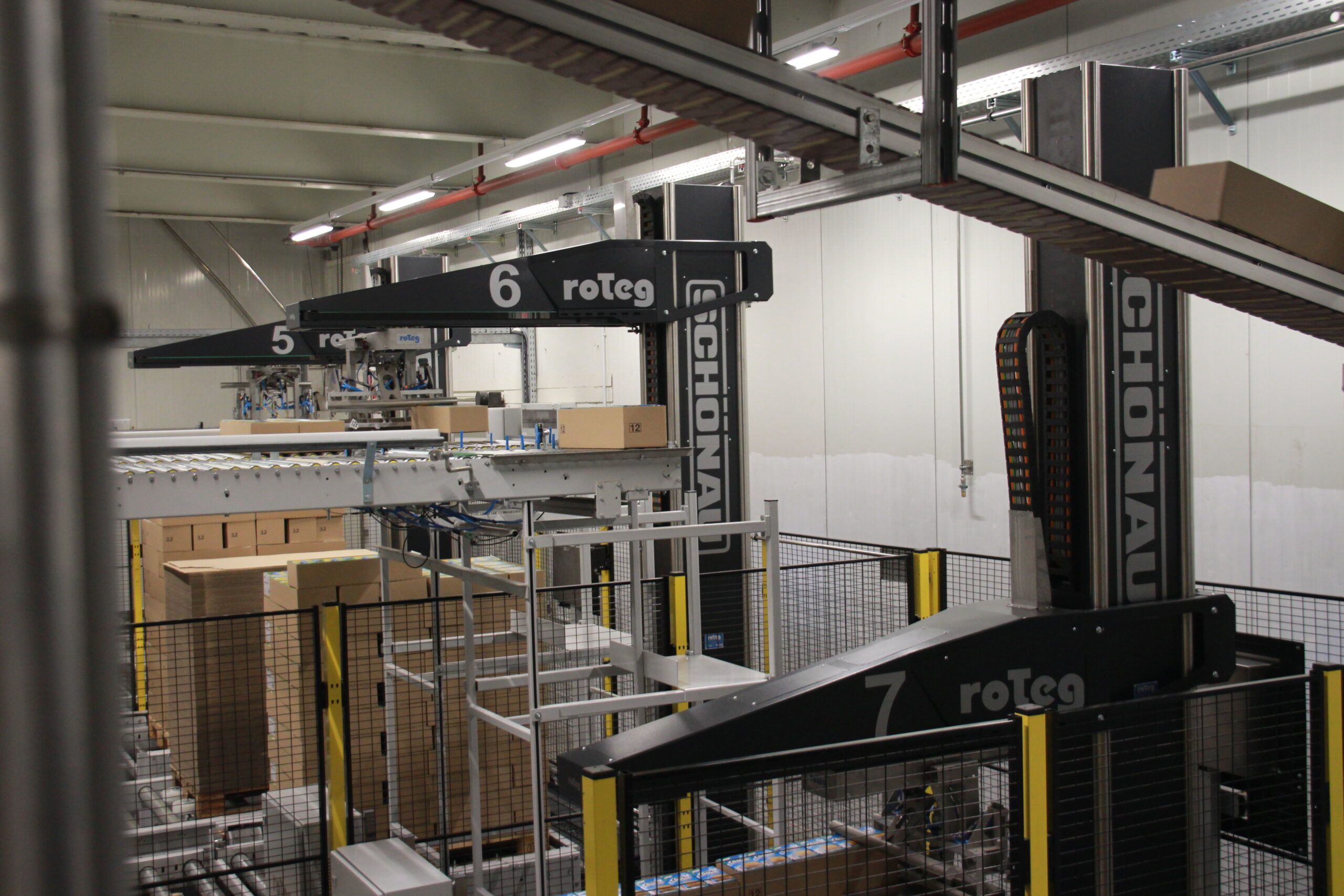
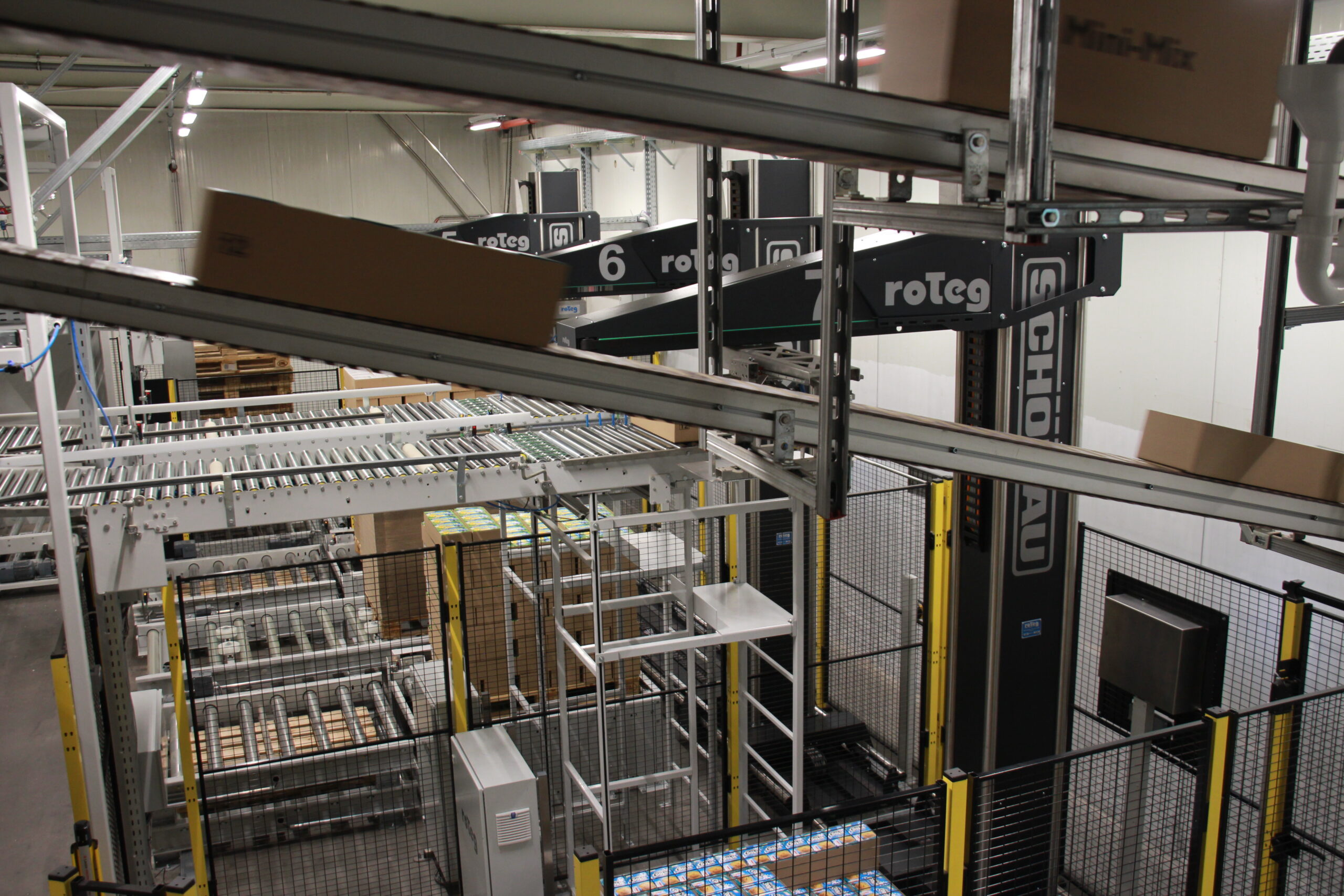
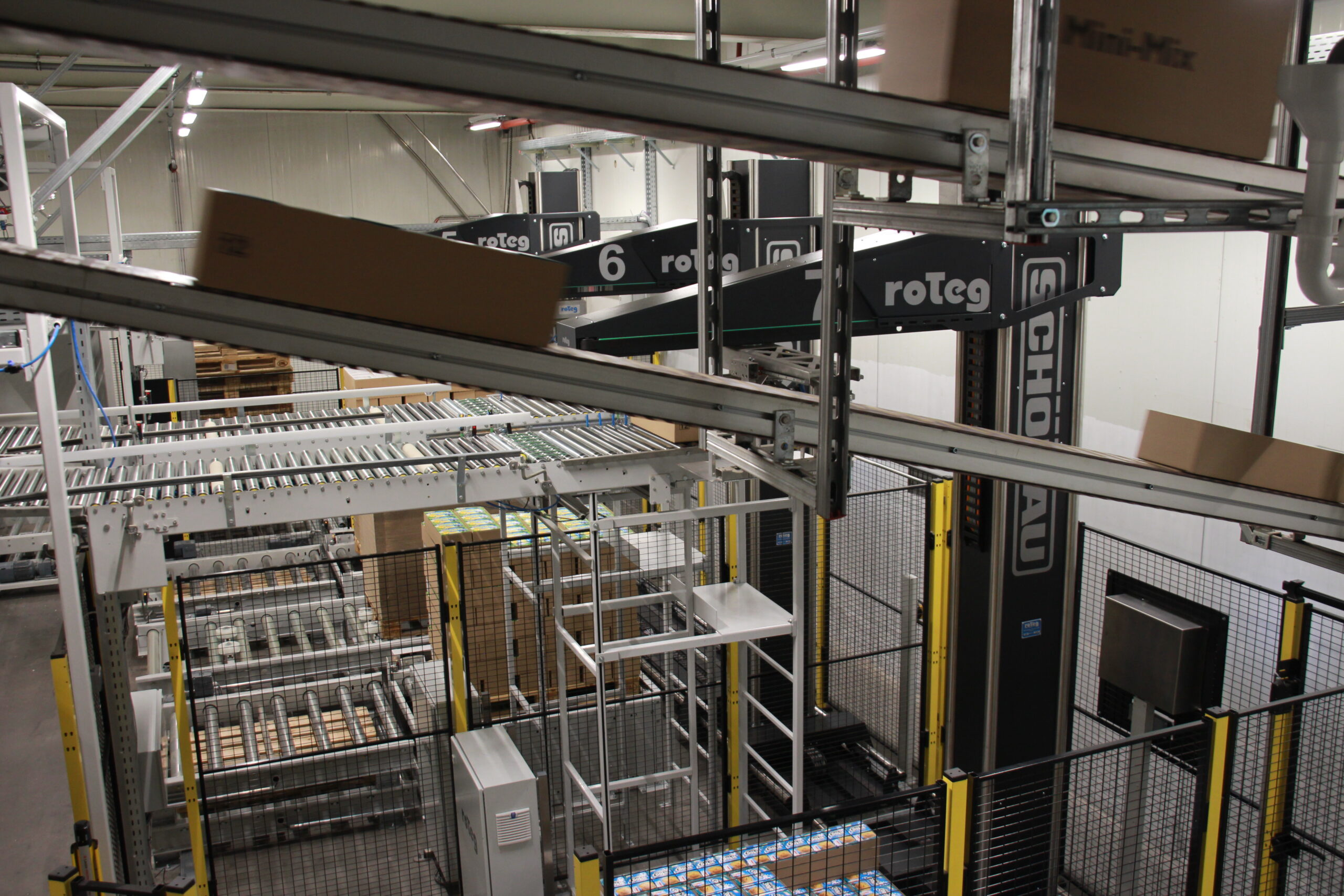
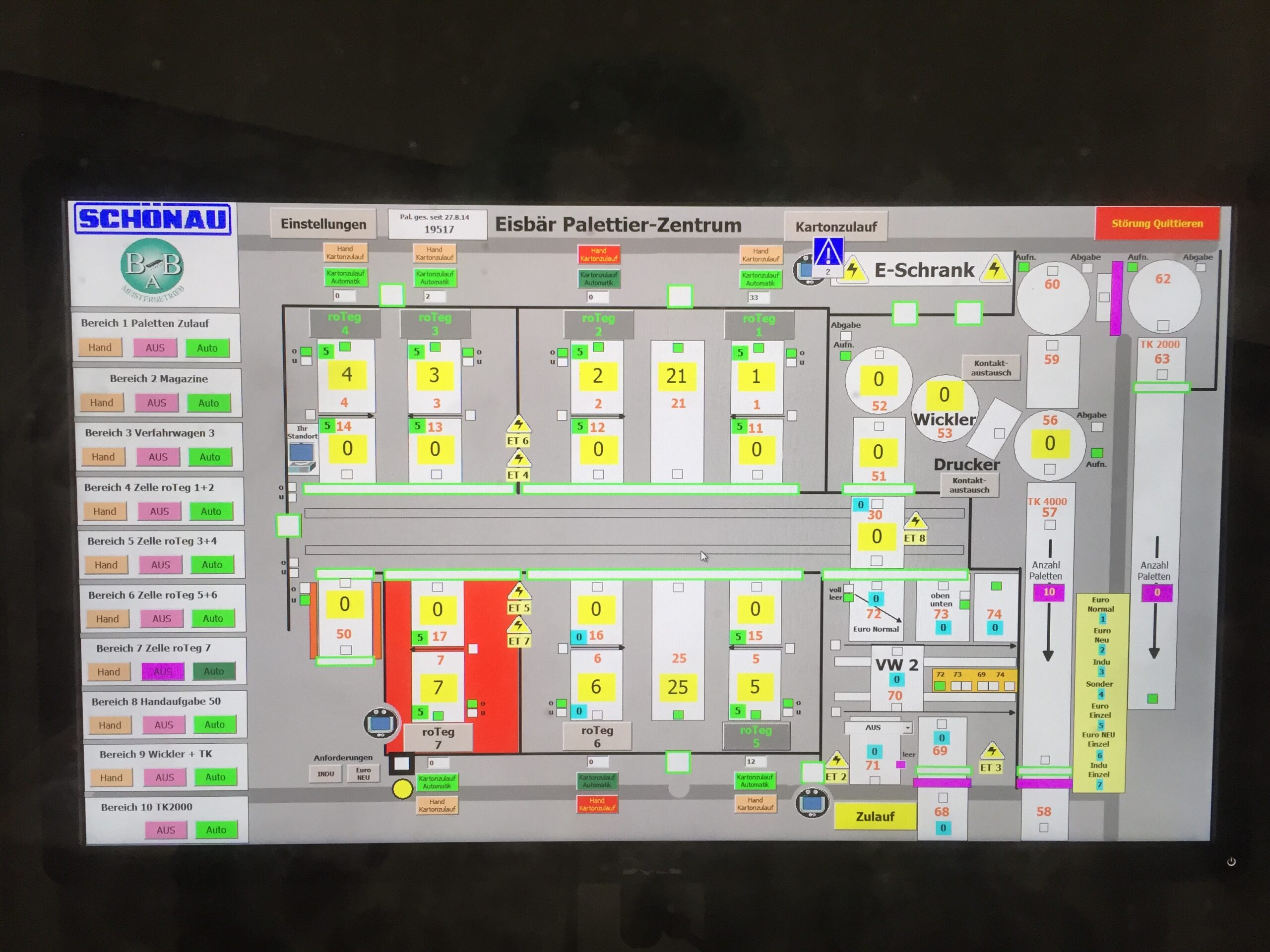
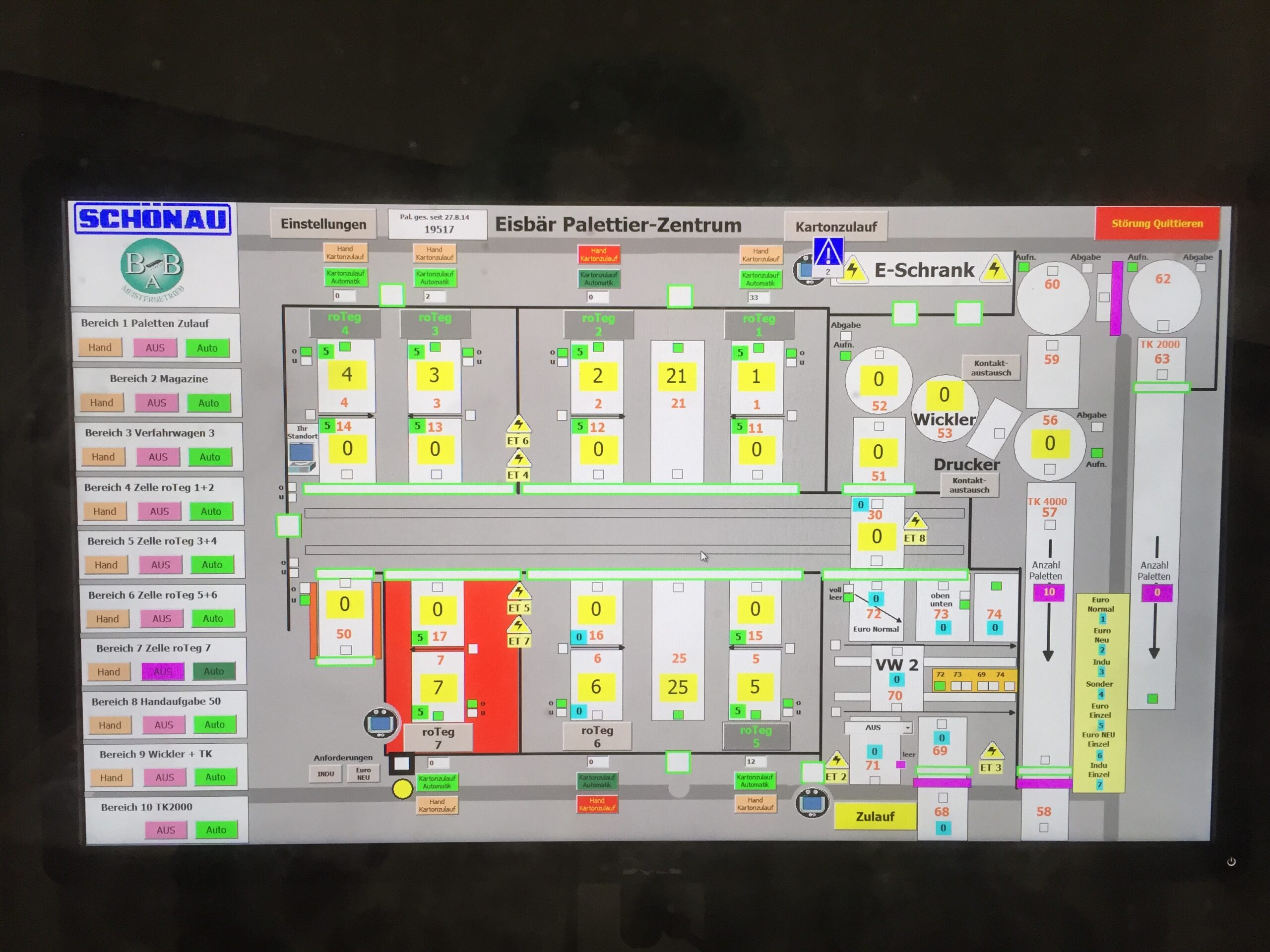
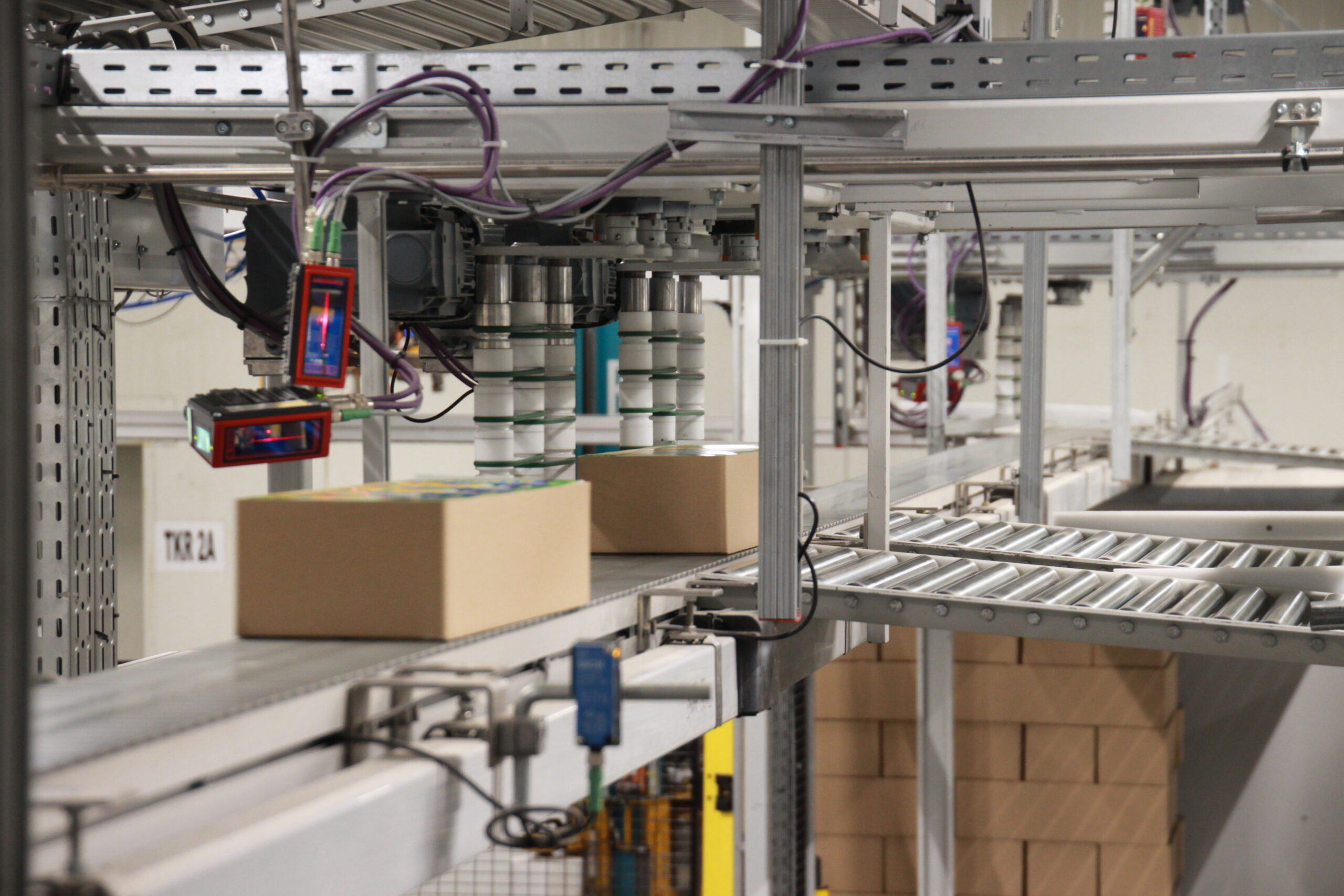
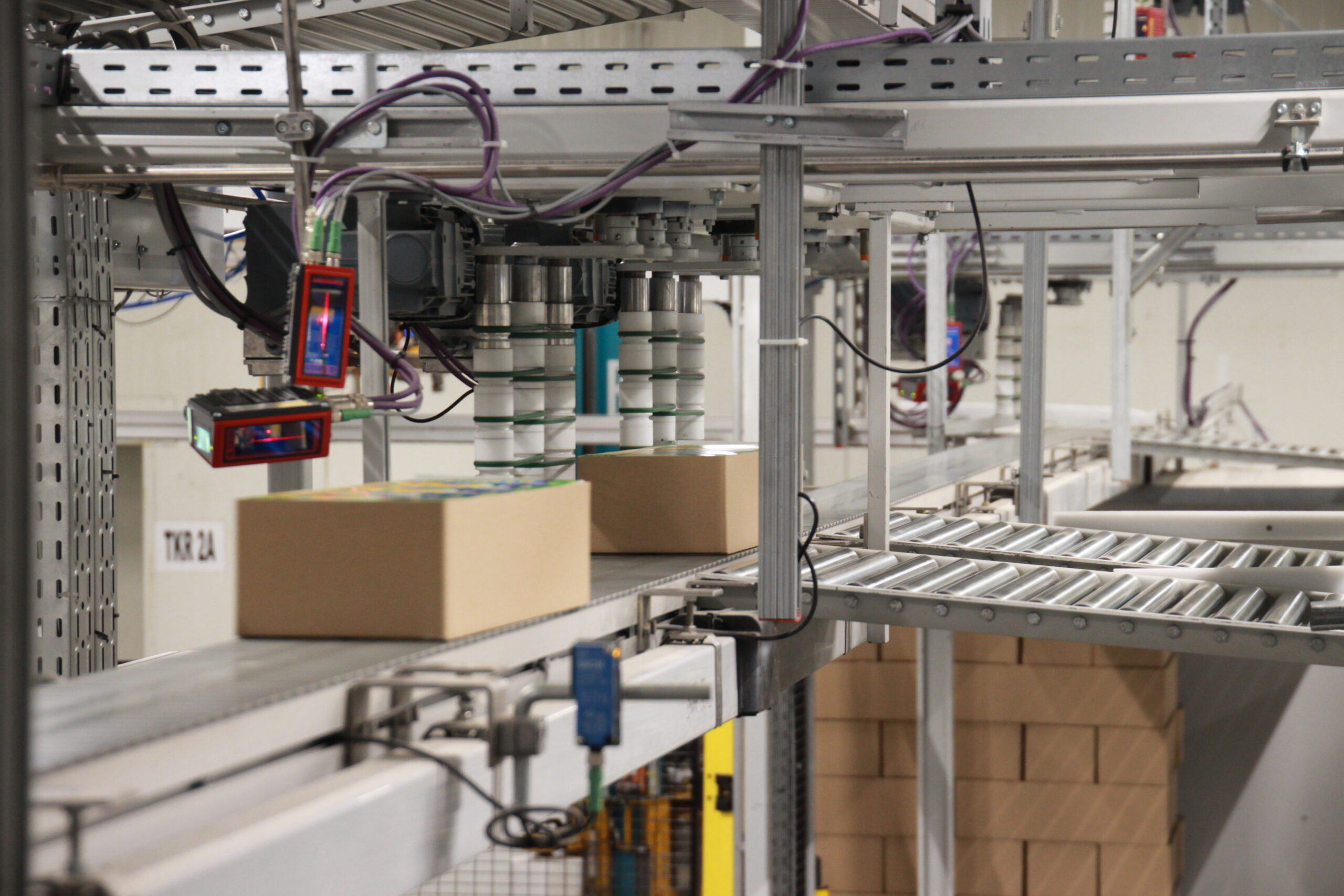
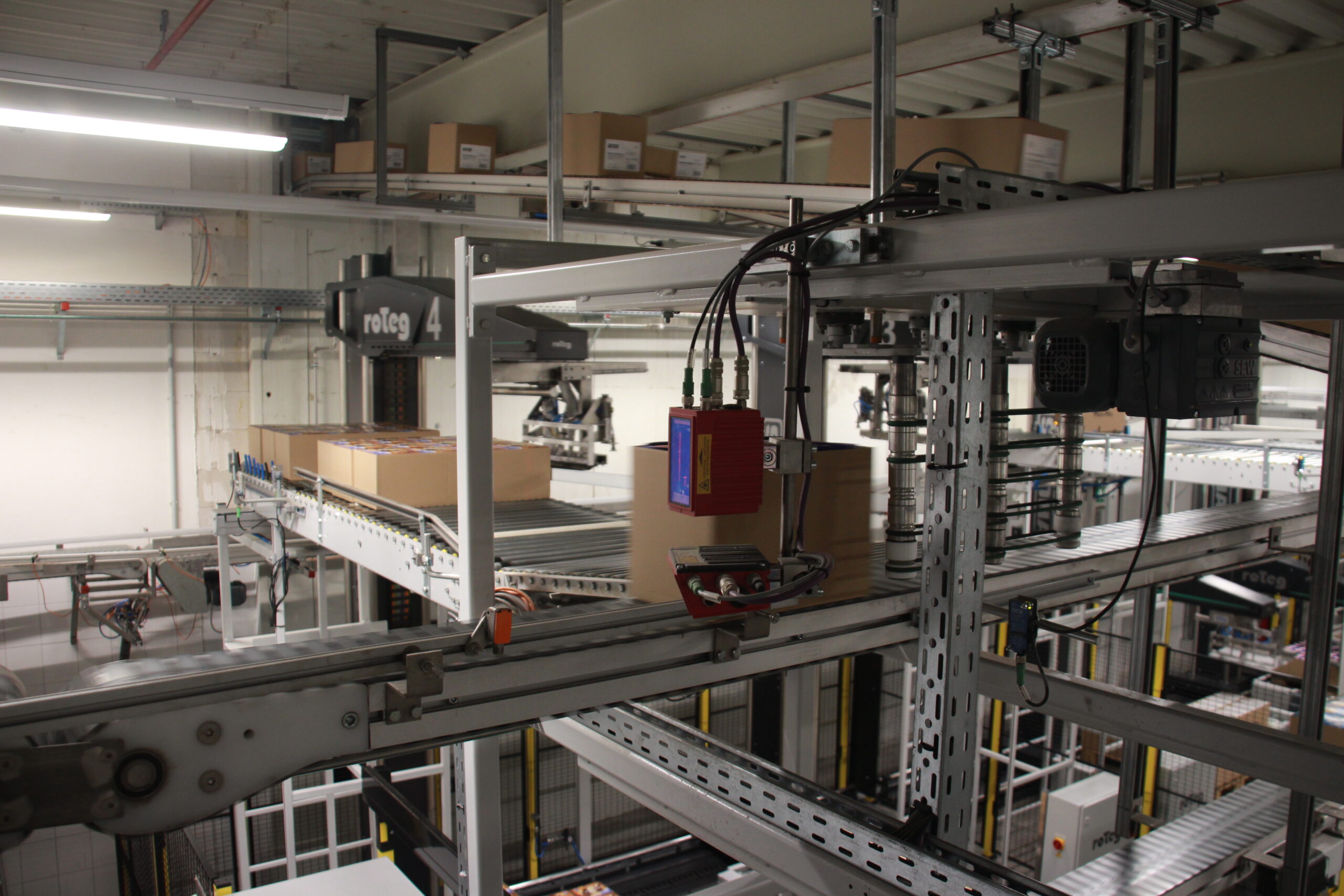
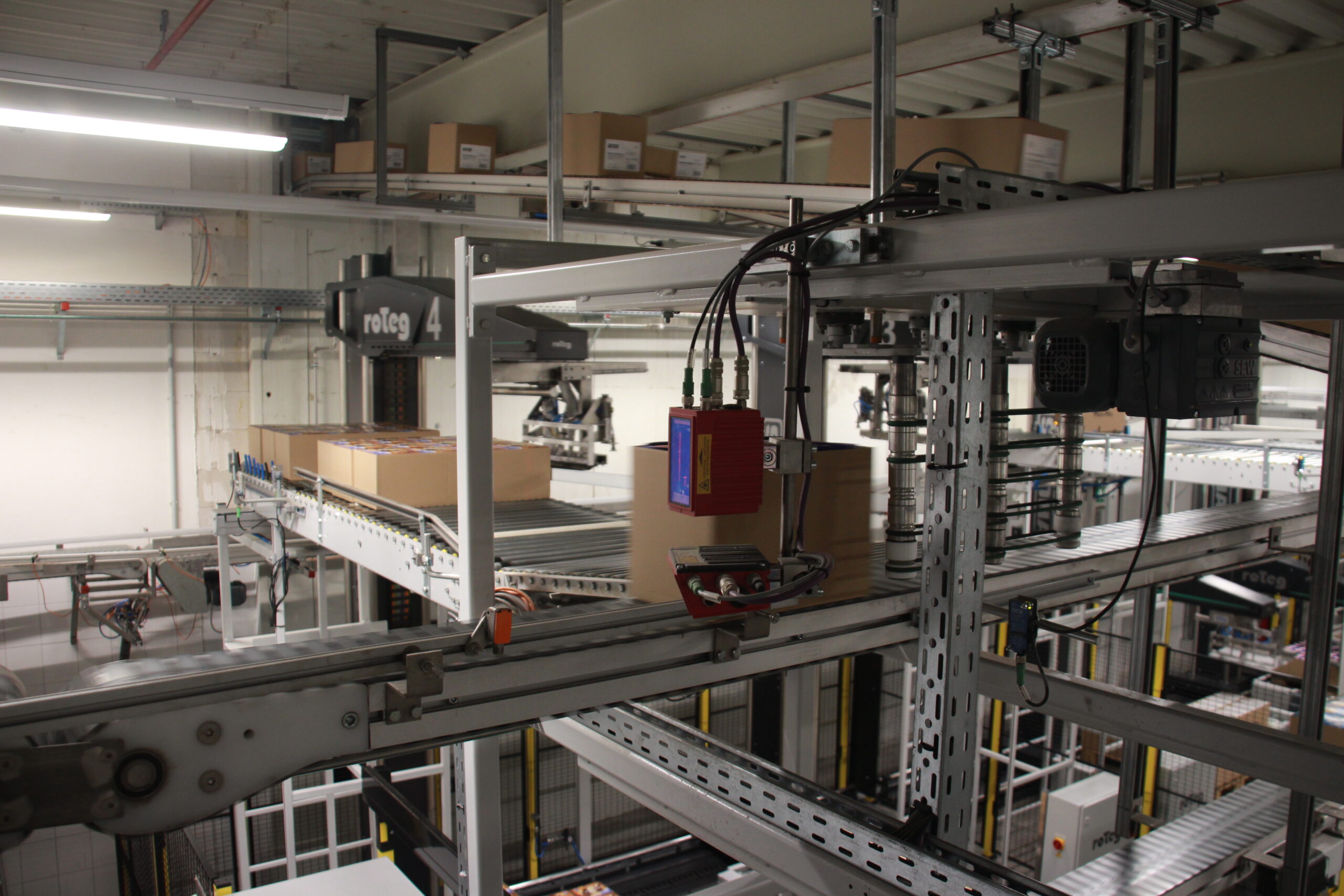
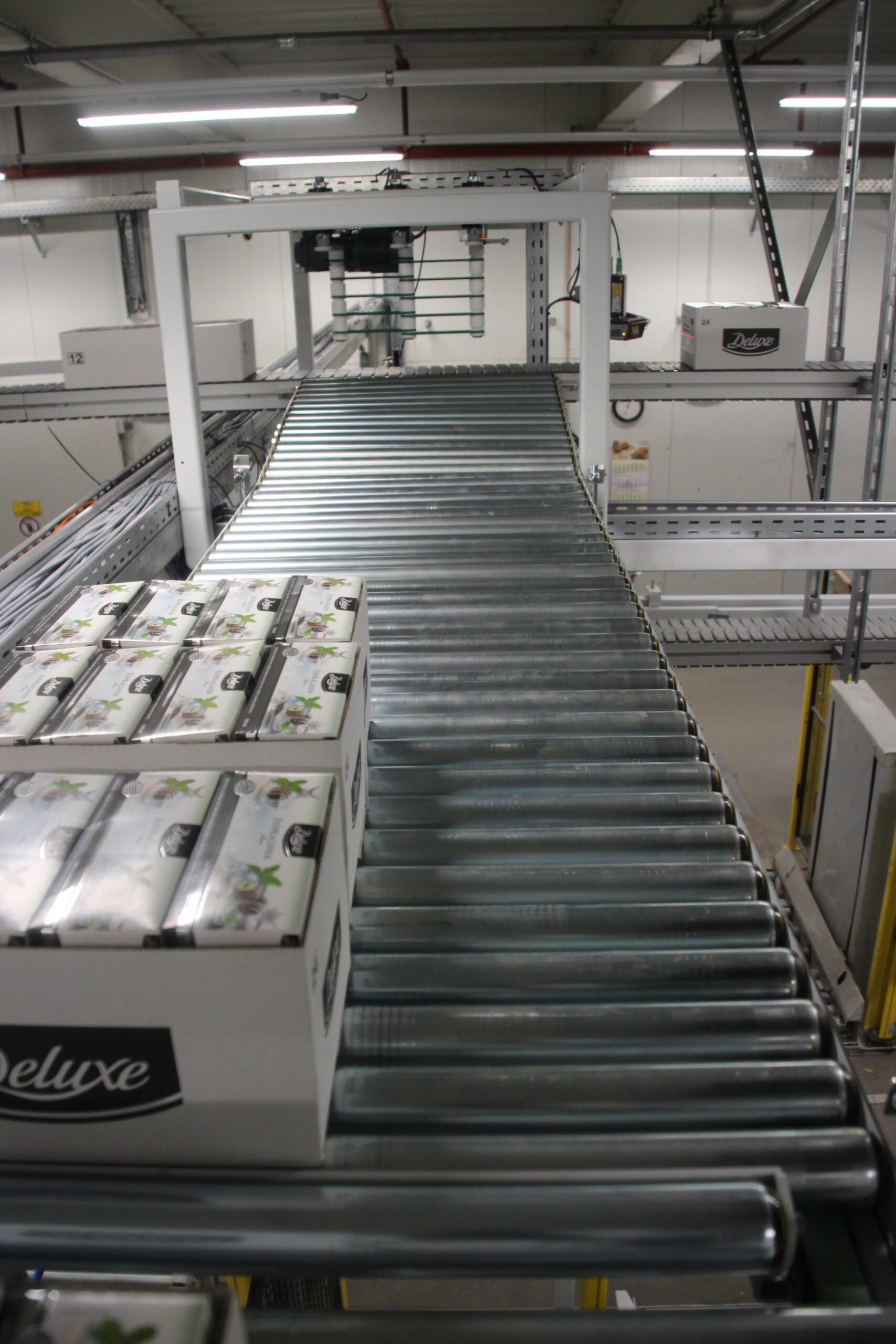
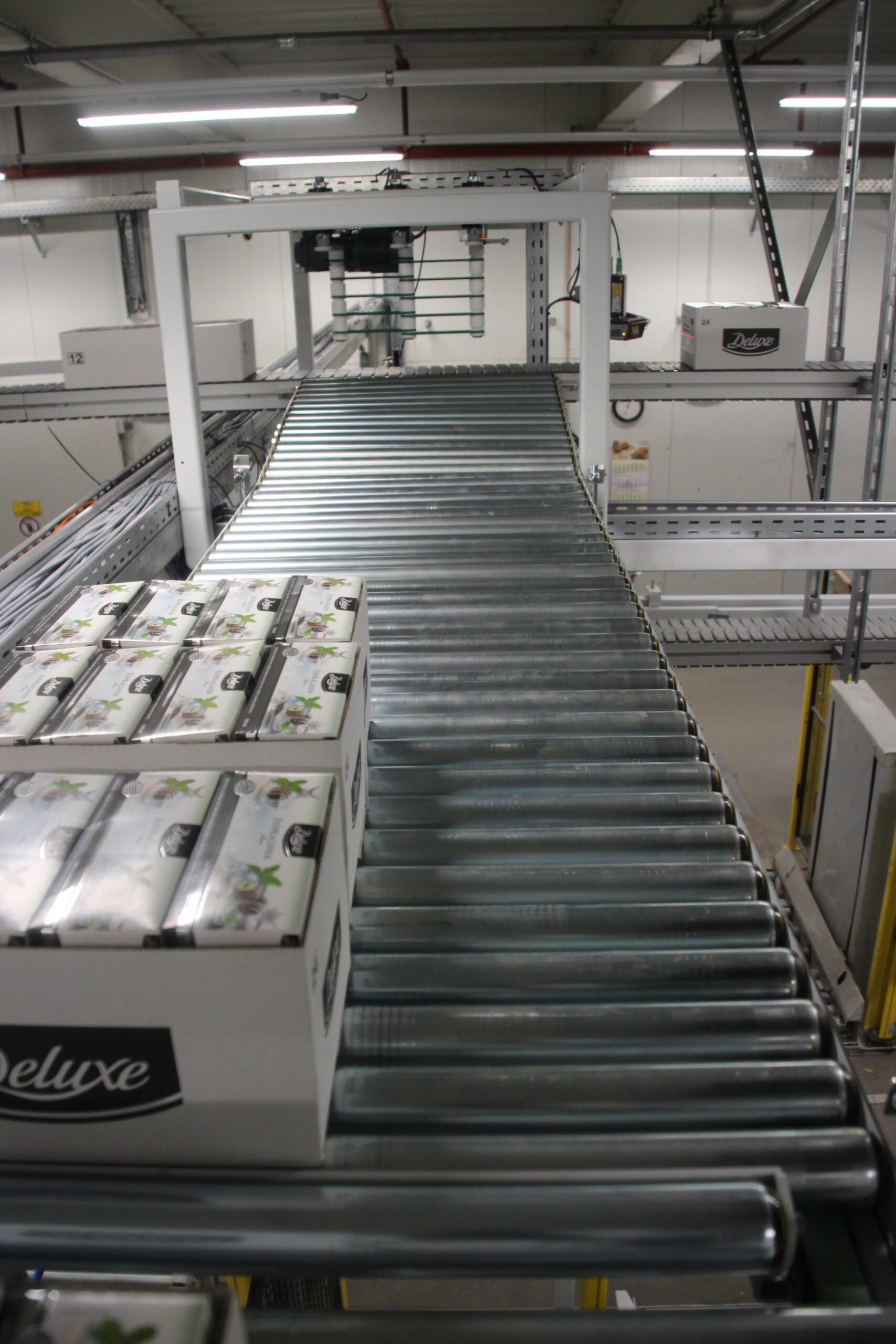
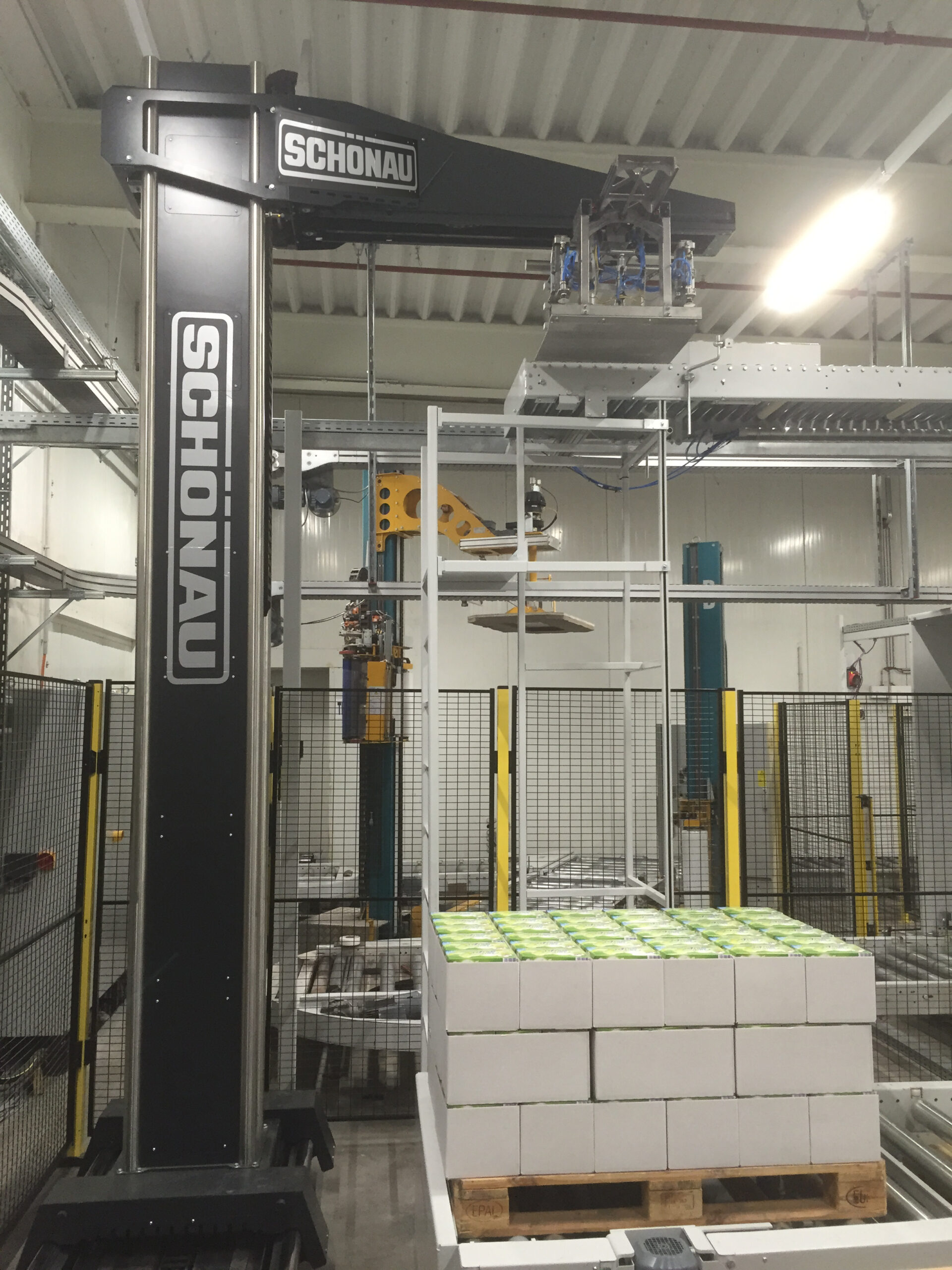
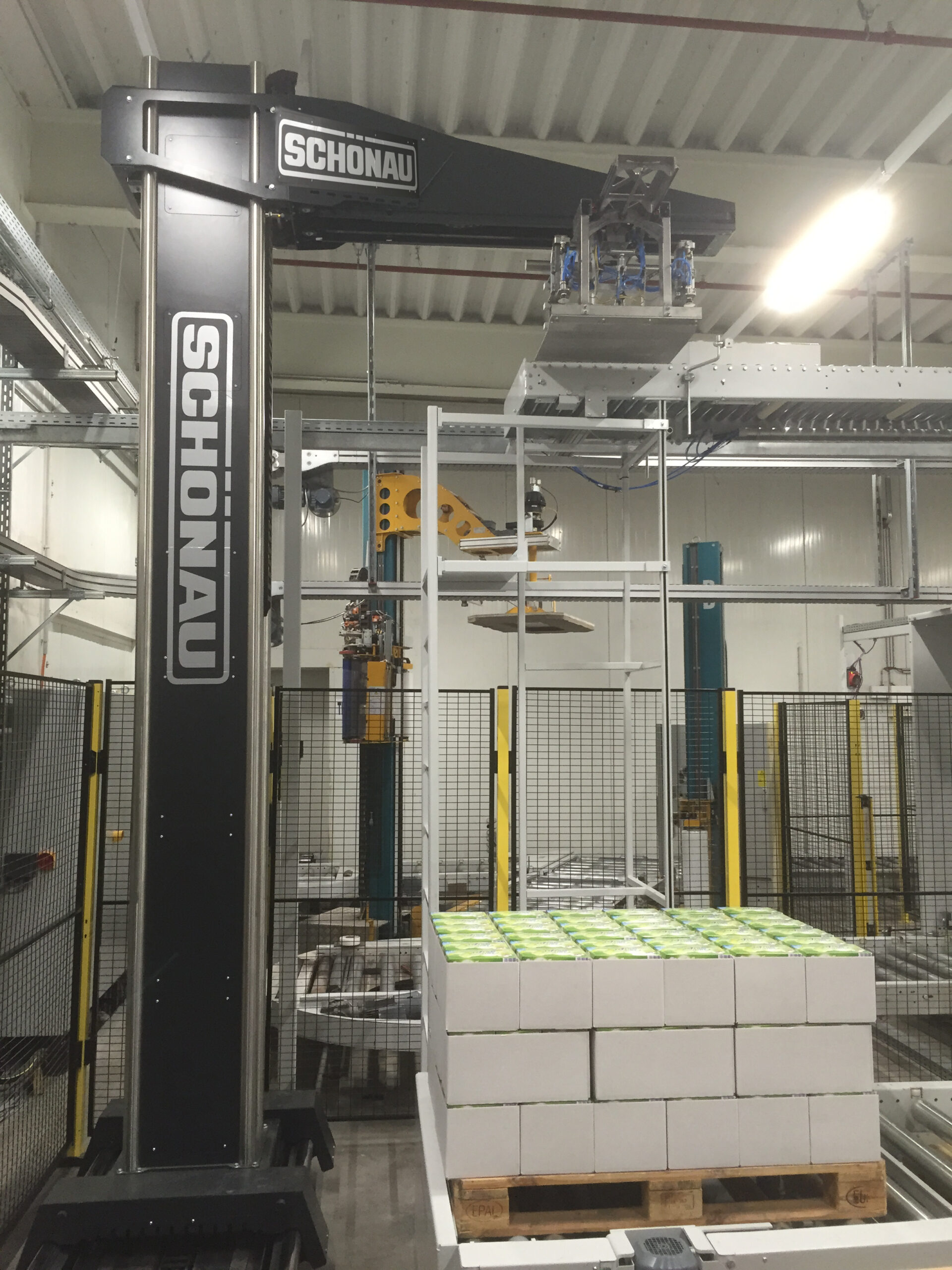
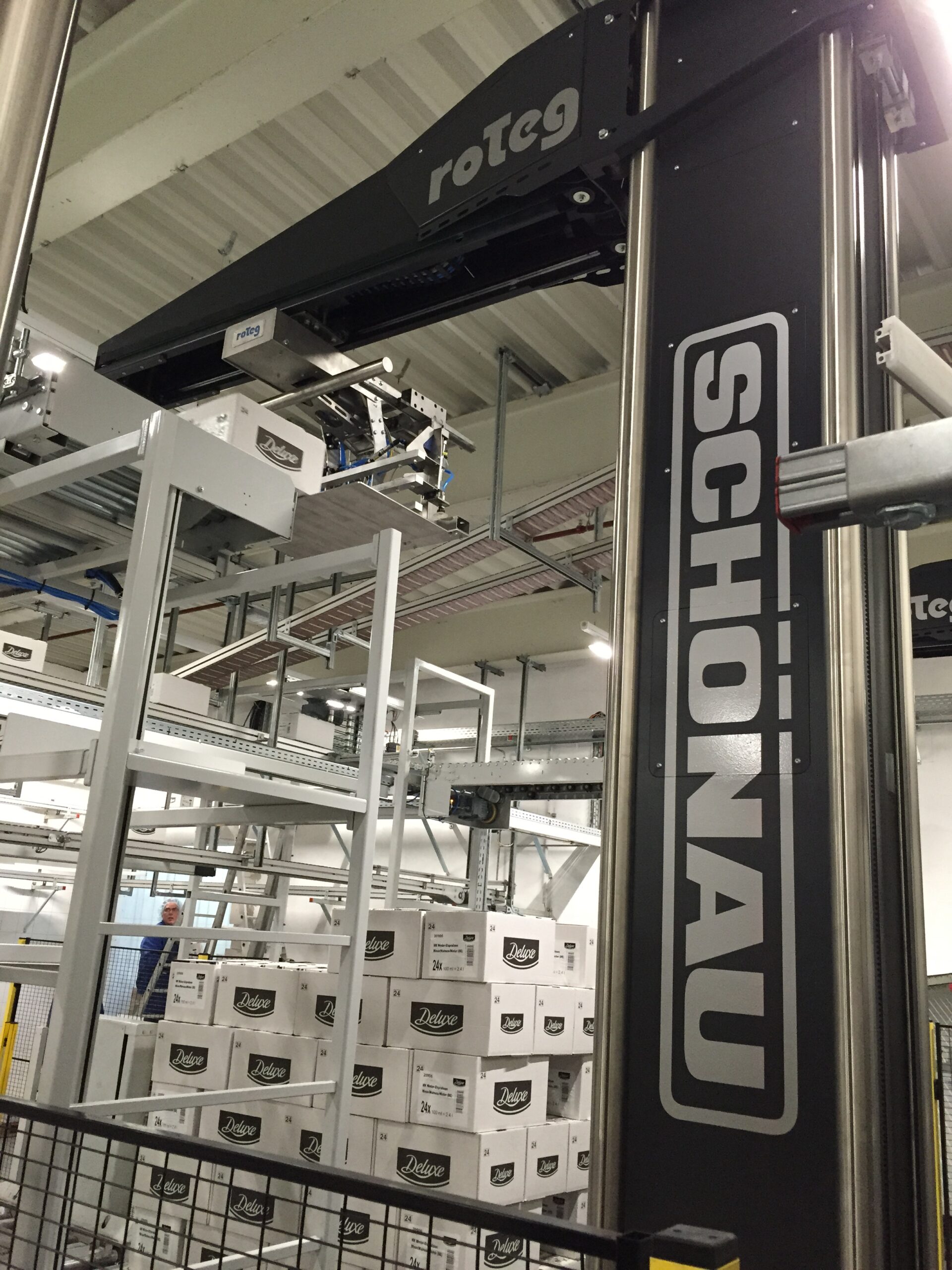
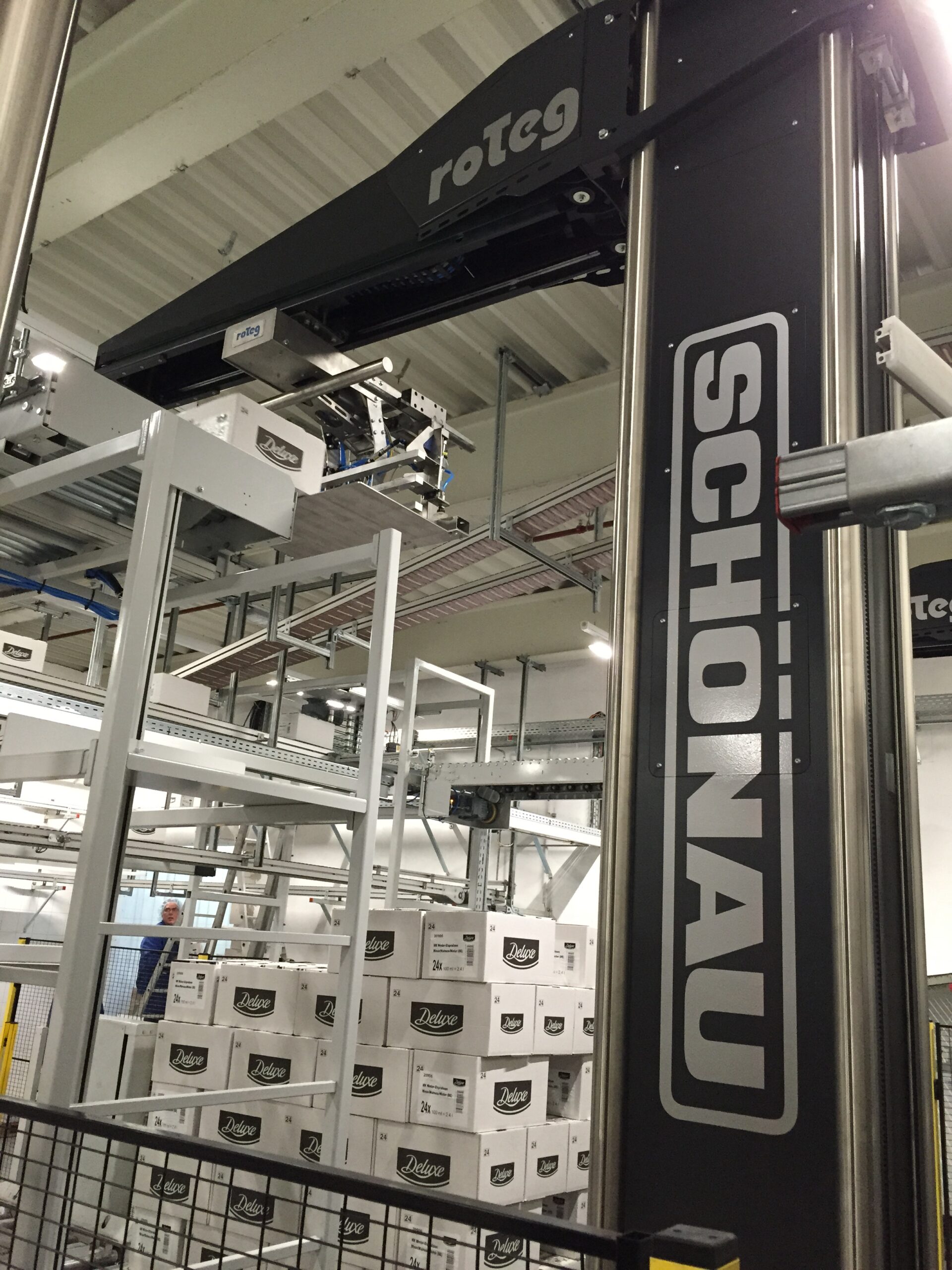
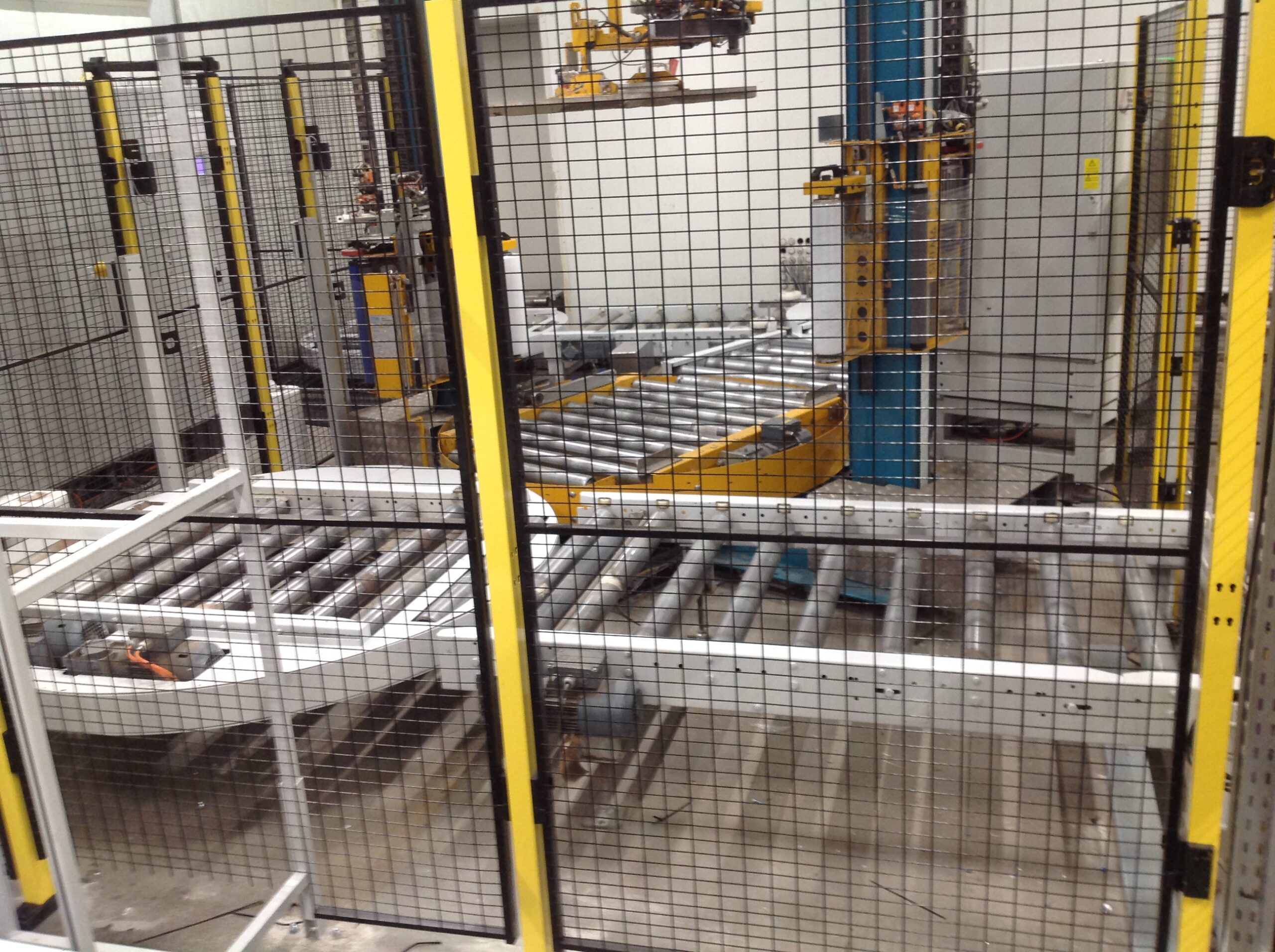
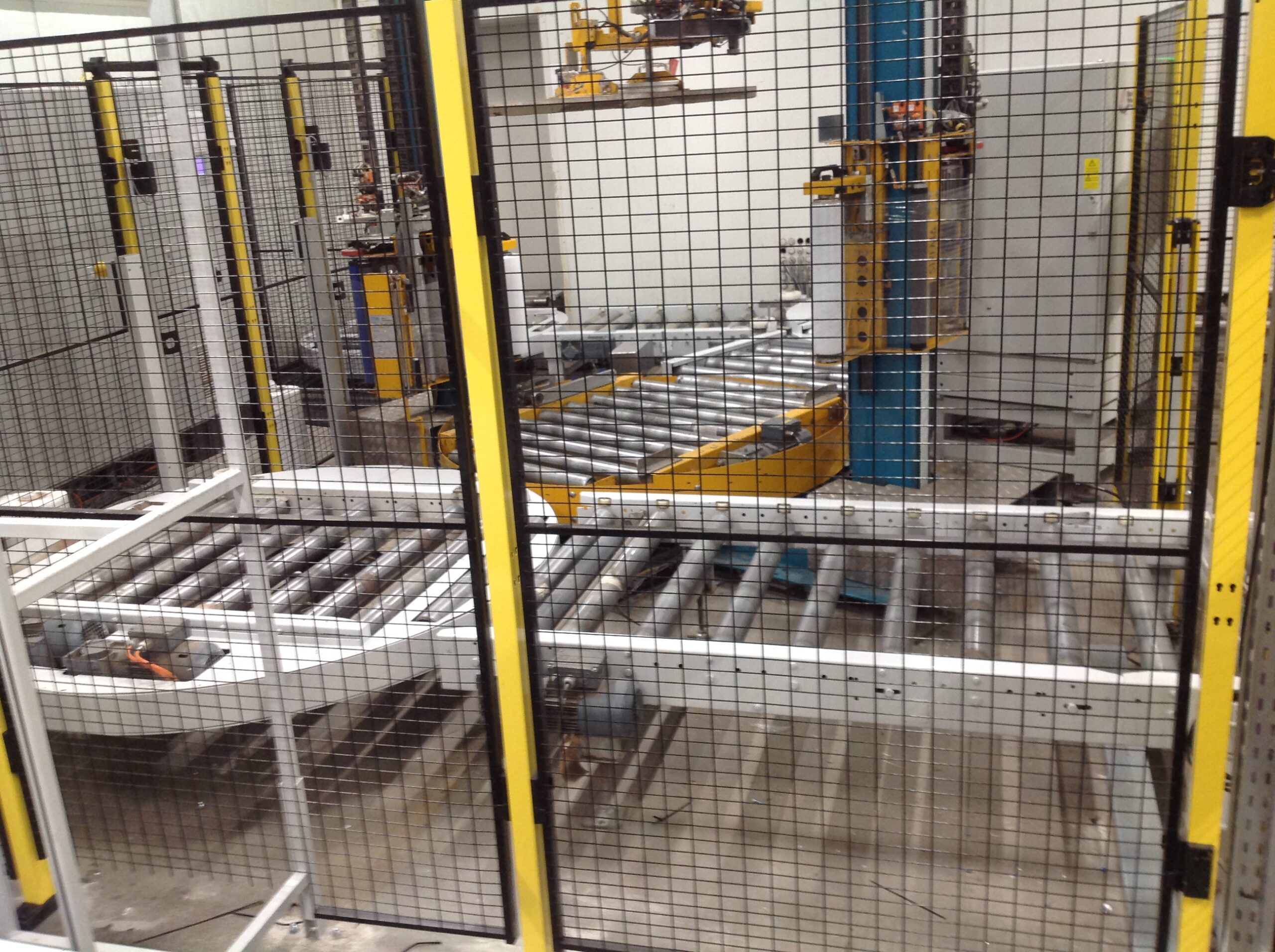
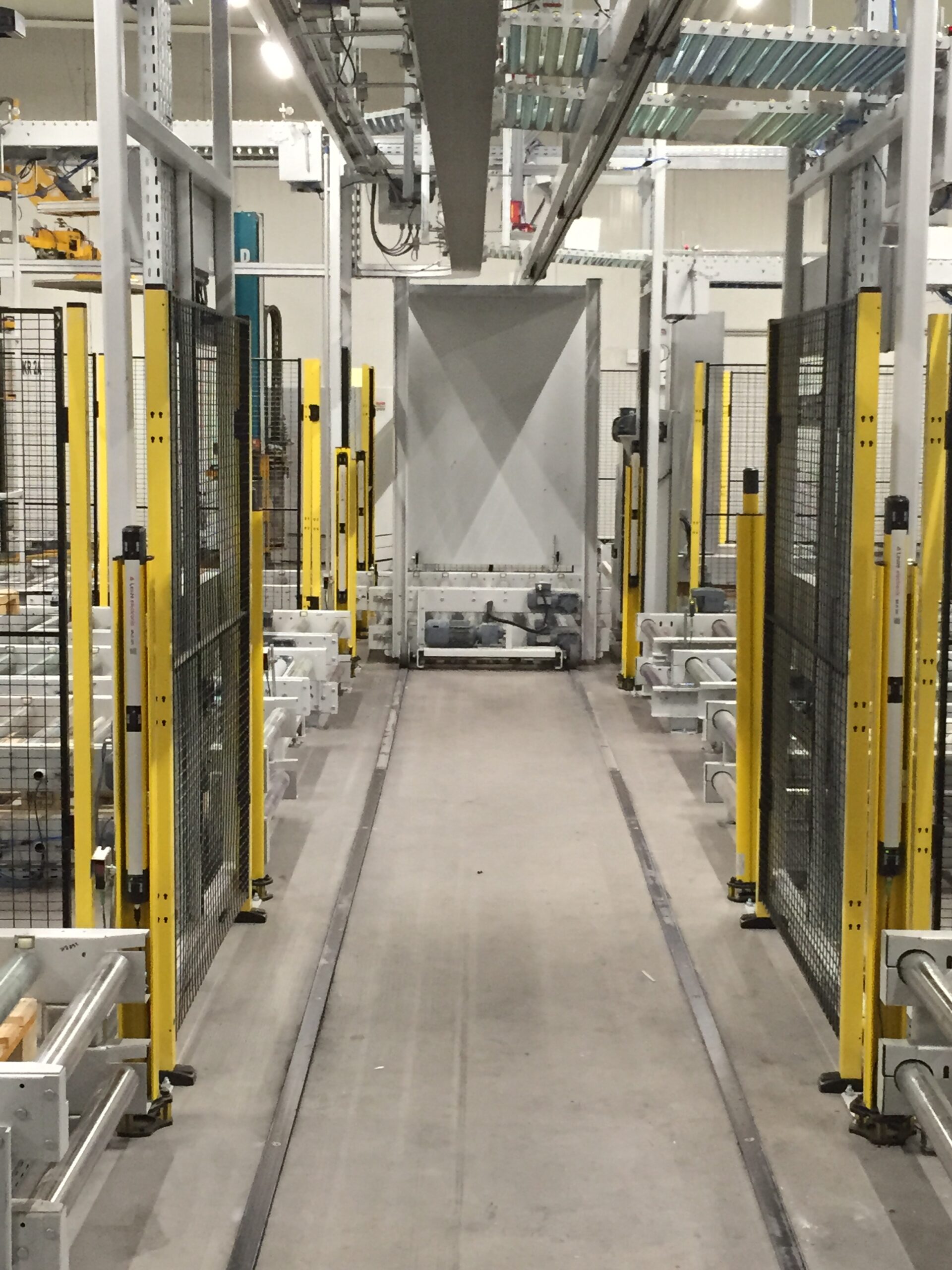
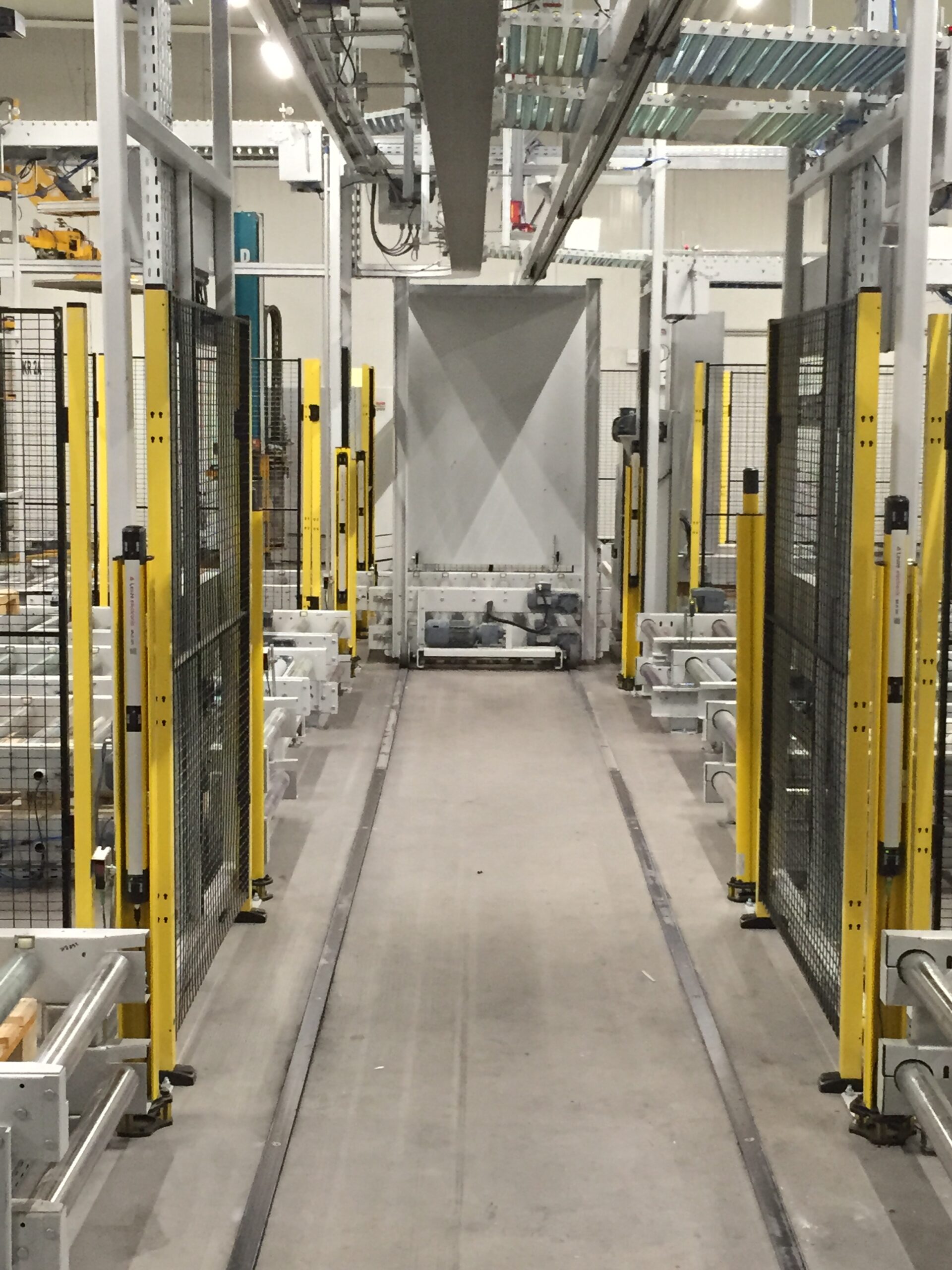