Referenzprojekt: AVG
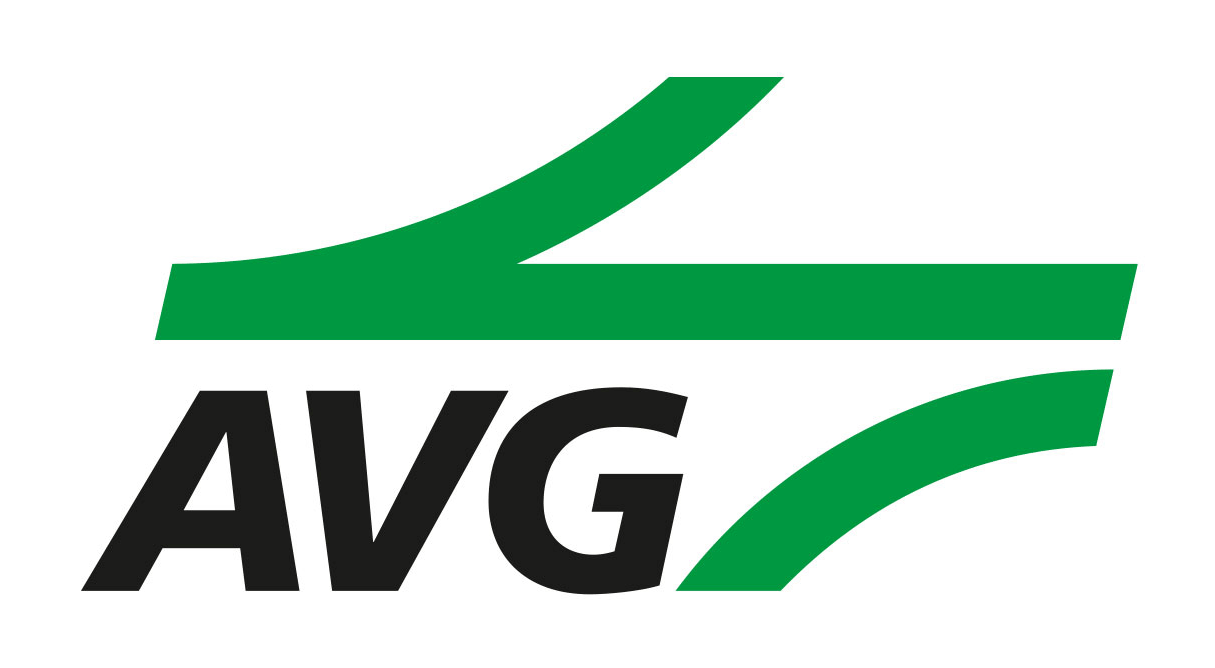
AVG Abfall-Verwertungs-Gesellschaft mbH, Hamburg
- Anlagennummer: 11836
Transportanlage für die Gebindebeschickung einer Müllverbrennungsanlage.
Kundenbeschreibung:
Die AVG Abfall-Verwertungs-Gesellschaft mbH ist Teil der europaweit tätigen Indaver-Gruppe und betreibt am Standort Hamburg eines der modernsten Entsorgungszentren weltweit. Im Fokus steht die sichere, nachhaltige und umweltverträgliche Behandlung gefährlicher und ungefährlicher Abfälle aus Industrie und öffentlichem Sektor.
Zentrales Element ist die Hochtemperaturverbrennungsanlage, mit einer Kapazität von 100.000 Tonnen pro Jahr. Die bei der Sonderabfallverbrennung gewonnene Abwärme wird über ein benachbartes Heizkraftwerk dem Hamburger Fernwärmenetz zugeführt – ein konsequenter Beitrag zur energetischen Verwertung und CO₂-Reduktion.
Projekt: Erneuerung der Zuführungstechnik für Drehrohröfen
Nach rund 30 Jahren Betriebszeit wurde die bestehende Technik zur Zuführung von Großgebinden vollständig rückgebaut und durch eine hochmoderne, flexible Förderlösung ersetzt. Ziel war es, die Beschickung der Drehrohröfen an aktuelle Anforderungen der Prozesssicherheit, Flexibilität und Automatisierung anzupassen.
Das neue System erlaubt eine differenzierte Vorlagerung und Zuführung unterschiedlicher Gebindearten – z. B. Fässer, Kanister, Hobbocks oder Eimer – entsprechend ihrer Belastungsklasse. Die automatische Steuerung erfolgt auf Basis eines Verbrennungsplans sowie kontinuierlicher Emissionsüberwachung.
Technische Highlights & Sicherheitskonzept
Förder- und Steuerungstechnik:
- Pulkförderung: Batchweise Aufgabe nach Gebindeklassifizierung
- Gebindetypen: Fässer, Kanister, Eimer etc. bis 300 kg
- Max. Maße je Gebinde: 700 × 700 × 1.000 mm
- Leistung: Bis zu 16 Gebinde pro Stunde und Ofen
- Pufferspeicher: >60 Gebinde – ermöglicht 2 Stunden autarken Betrieb
- Wiegezellen: Erfassen präzise die zugeführte Abfallmenge je Ofen
- Teleskopförderer: Minimieren Übergabelücken, Übergabe an Rechen und Ofenheber
Ergonomie & Sicherheit:
- Gebindeheber: Ergonomische Aufgabehöhe für manuelle Bedienung
- Drehtische (teleskopierend): Beidseitig einsetzbar für flexible Anordnung
- STAHL-Bedienpulte: In ATEX-Ausführung für Hand- und Vor-Ort-Bedienung
- Sicherheitskonzept:
- Ex-Zonen-Ausführung nach ATEX-Richtlinie
- Gaswarnanlage zur Umgebungskontrolle
- Modifizierte Schutzzaunanlage mit Lichtschranken und kontaktgesicherten Zugangstüren
Prozessintegration:
- Steuerung über redundanten Profibus & Beckhoff-Klemmen
- Einbindung ins Prozessleitsystem ABB
- KKS-Kennzeichnung für vollständige technische Dokumentation
- Reintegration vorhandener Anlagenkomponenten zur Ressourcenschonung
Fazit
Dieses Projekt zeigt, wie SCHÖNAU technische Komplexität, Sicherheitsanforderungen und Nachhaltigkeitsziele miteinander vereint. Die neue Zuführtechnik der AVG Hamburg ist robust, flexibel und vollständig integriert – bereit für die nächsten Jahrzehnte sicherer Sonderabfallverwertung auf höchstem Niveau.
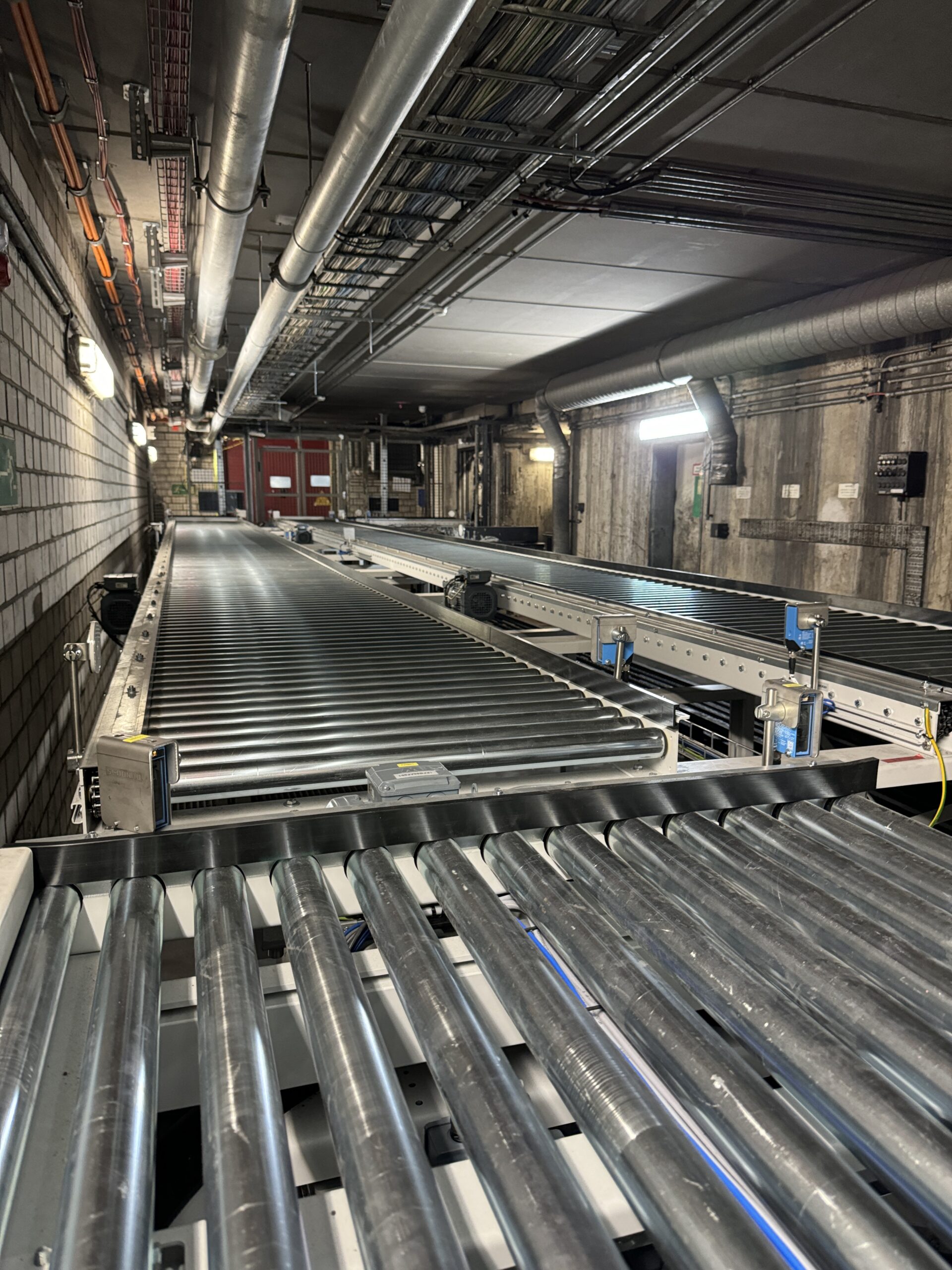
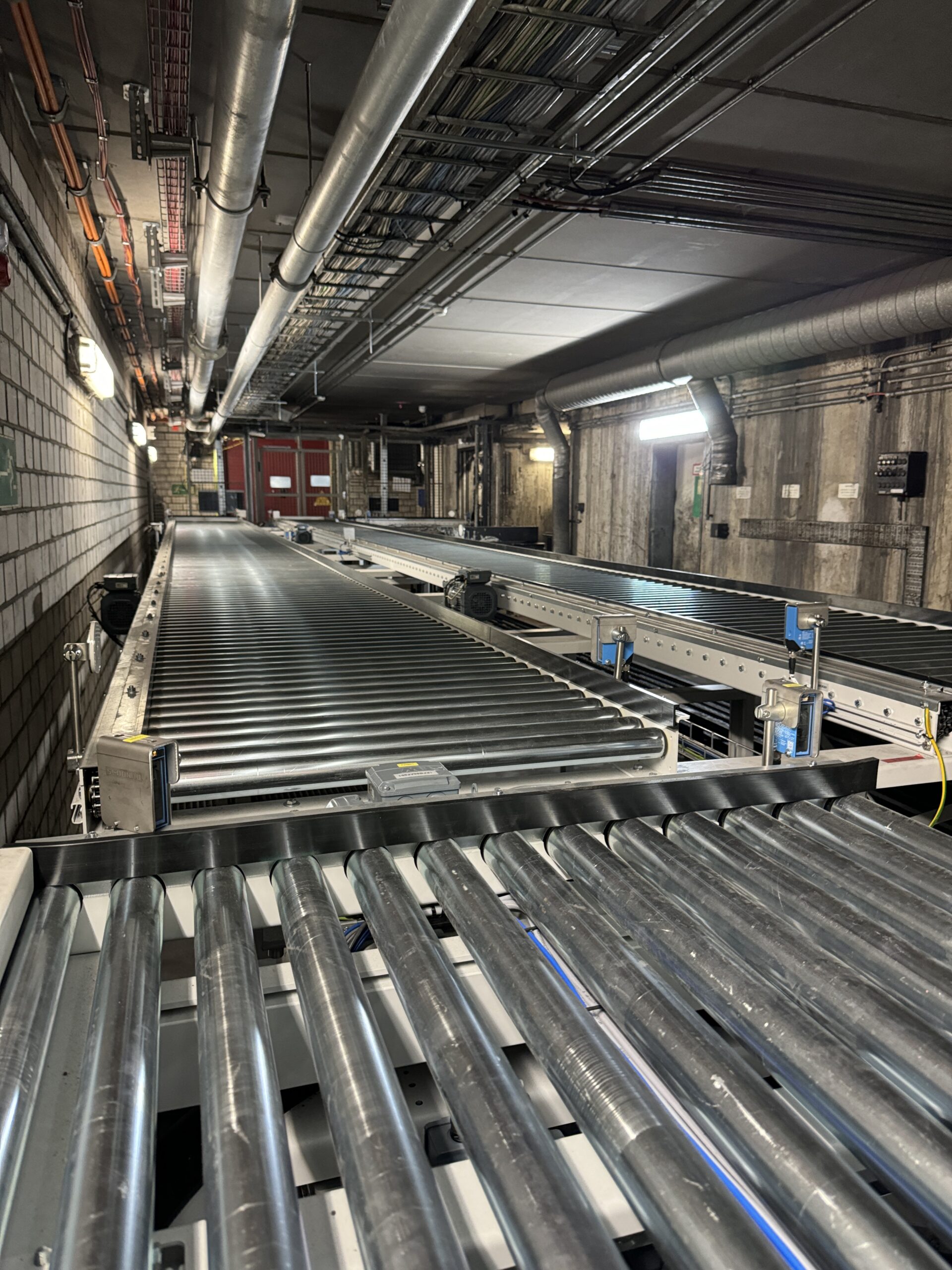
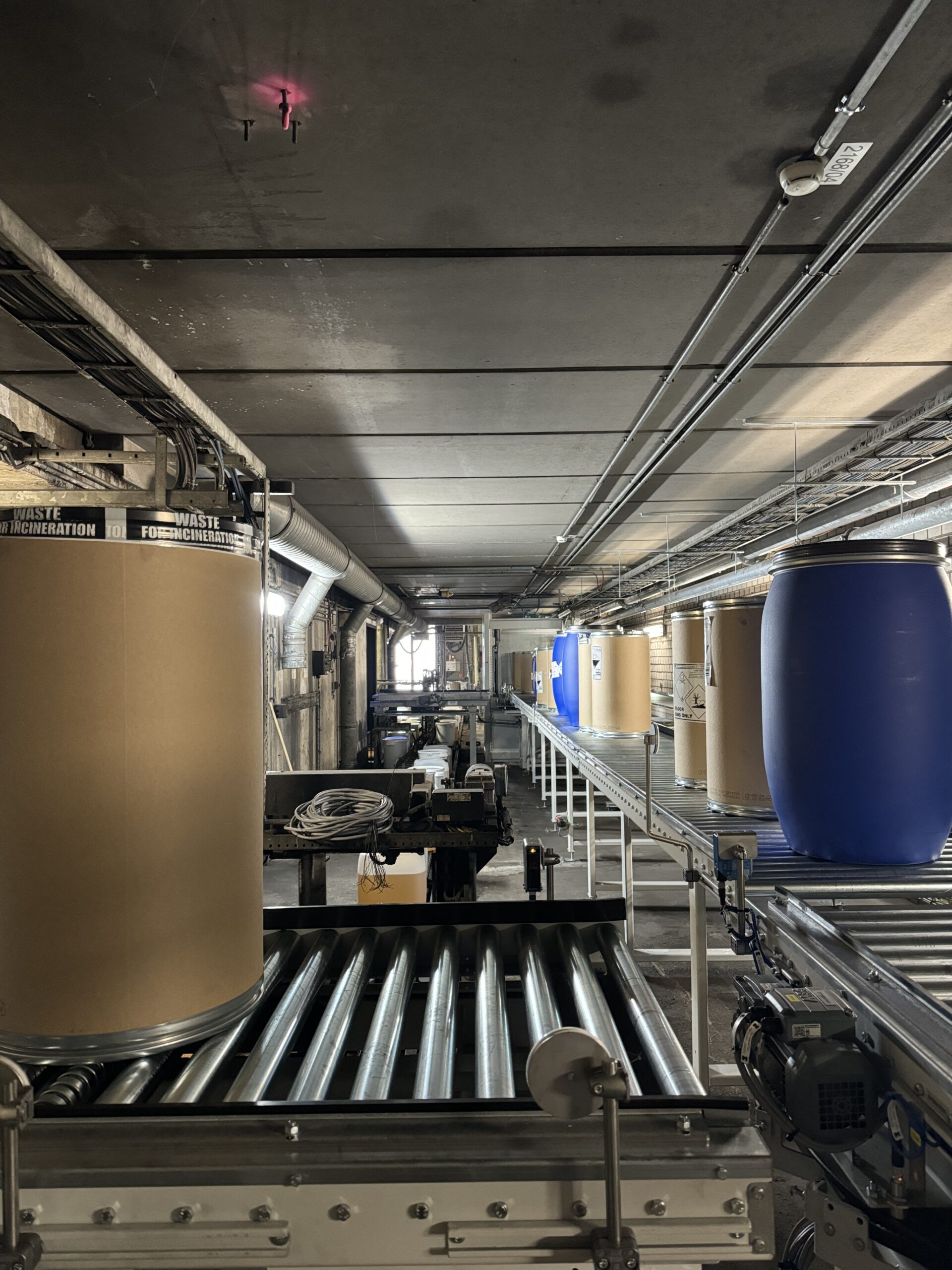
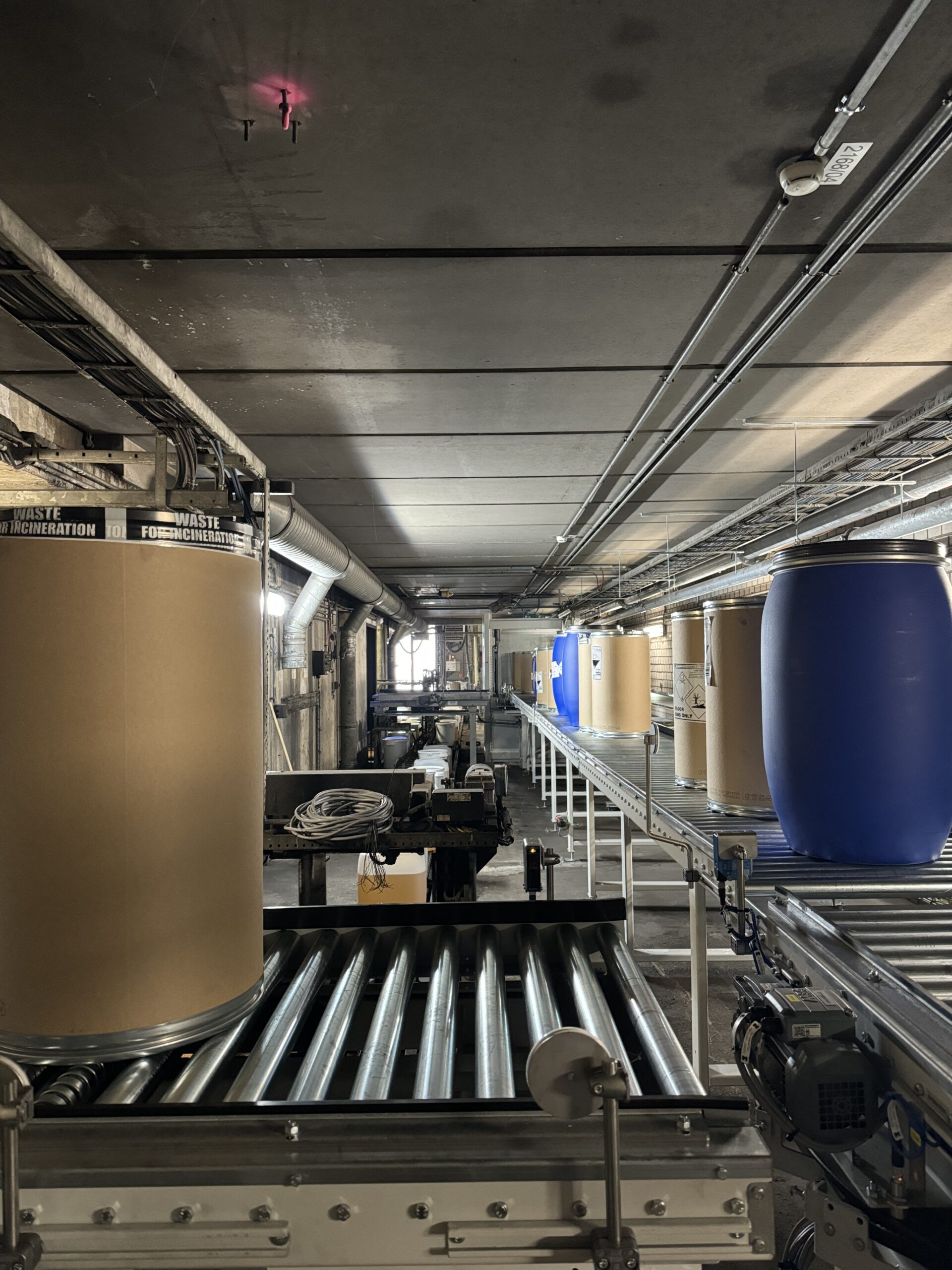
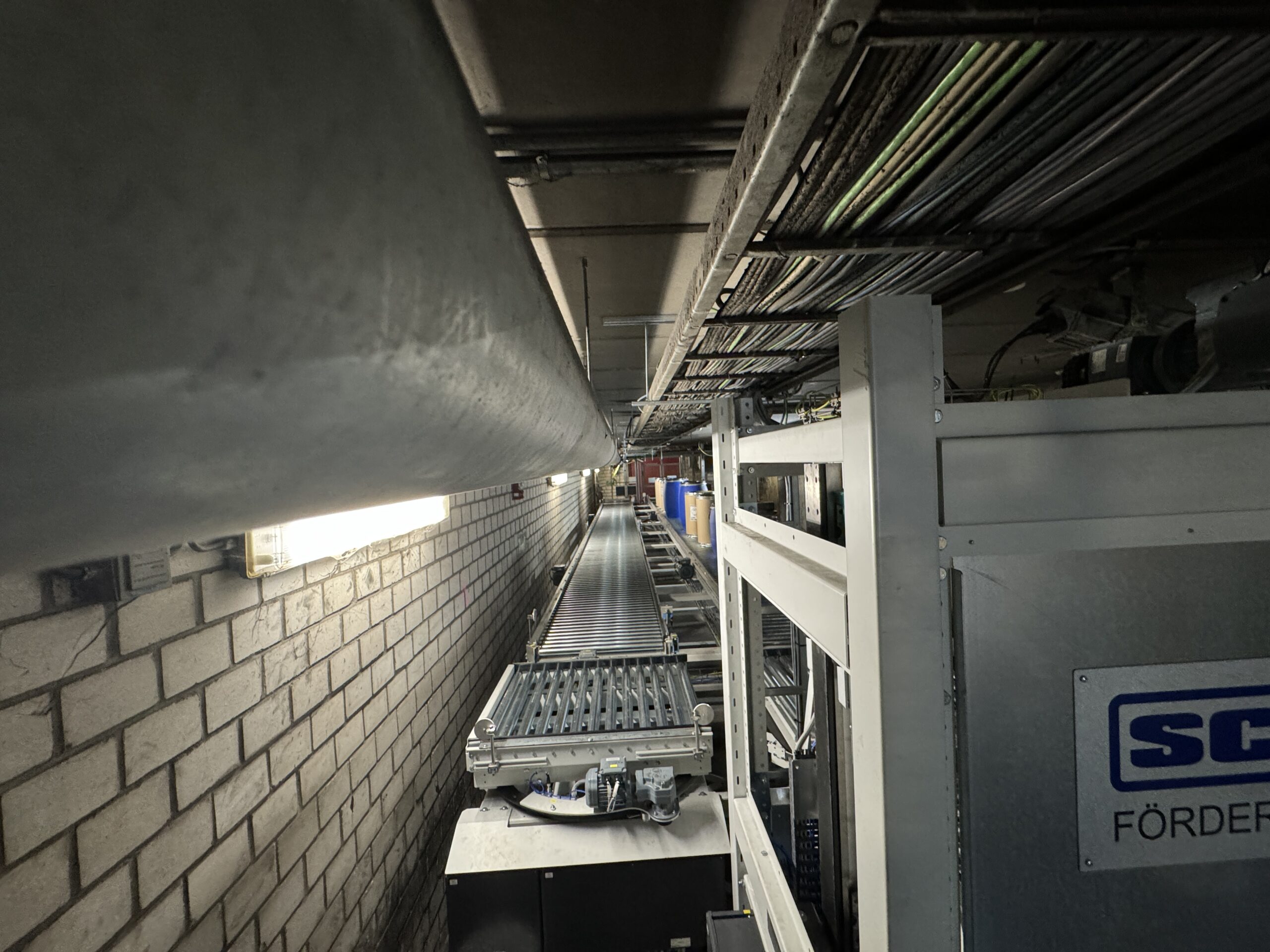
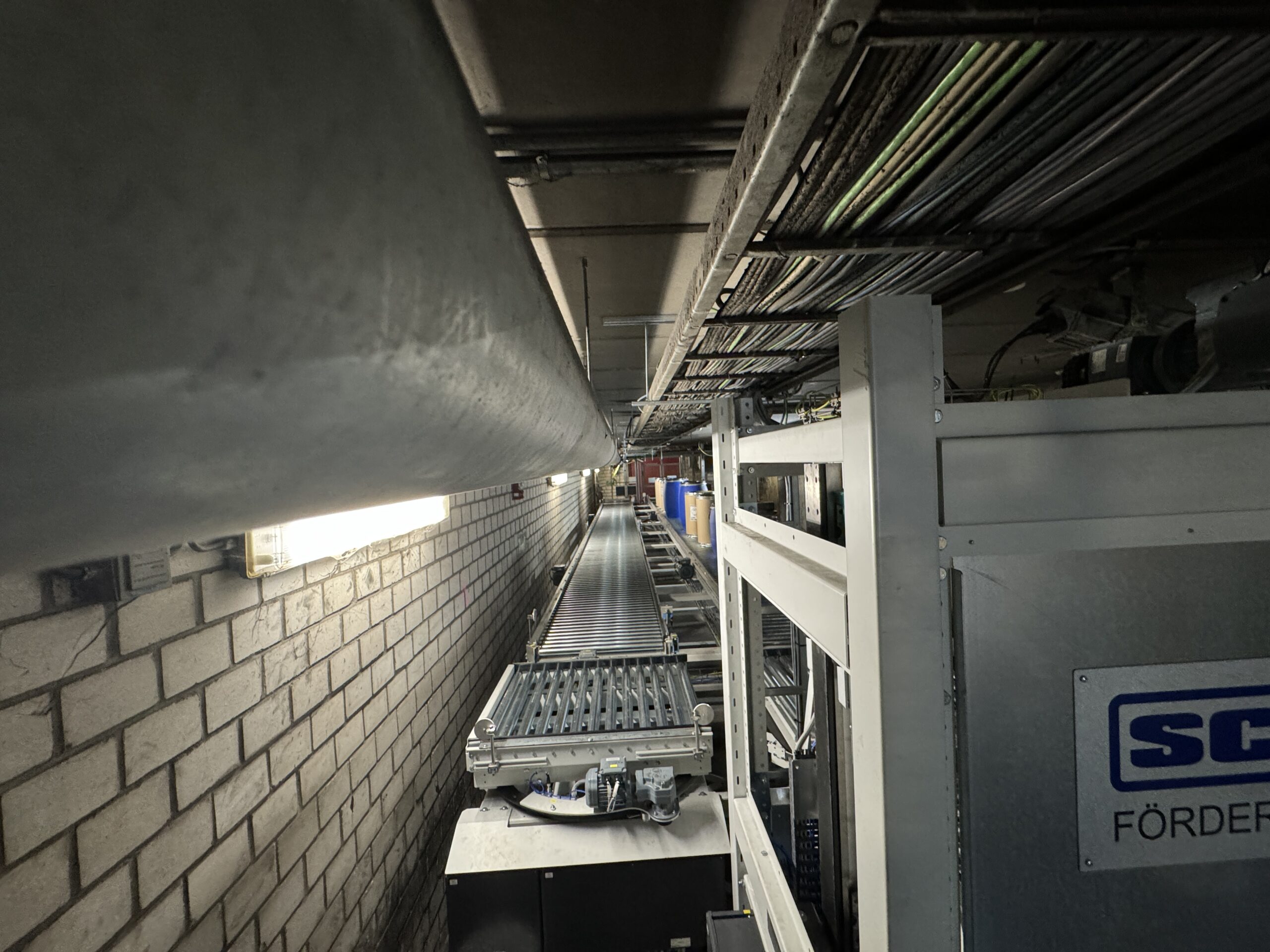
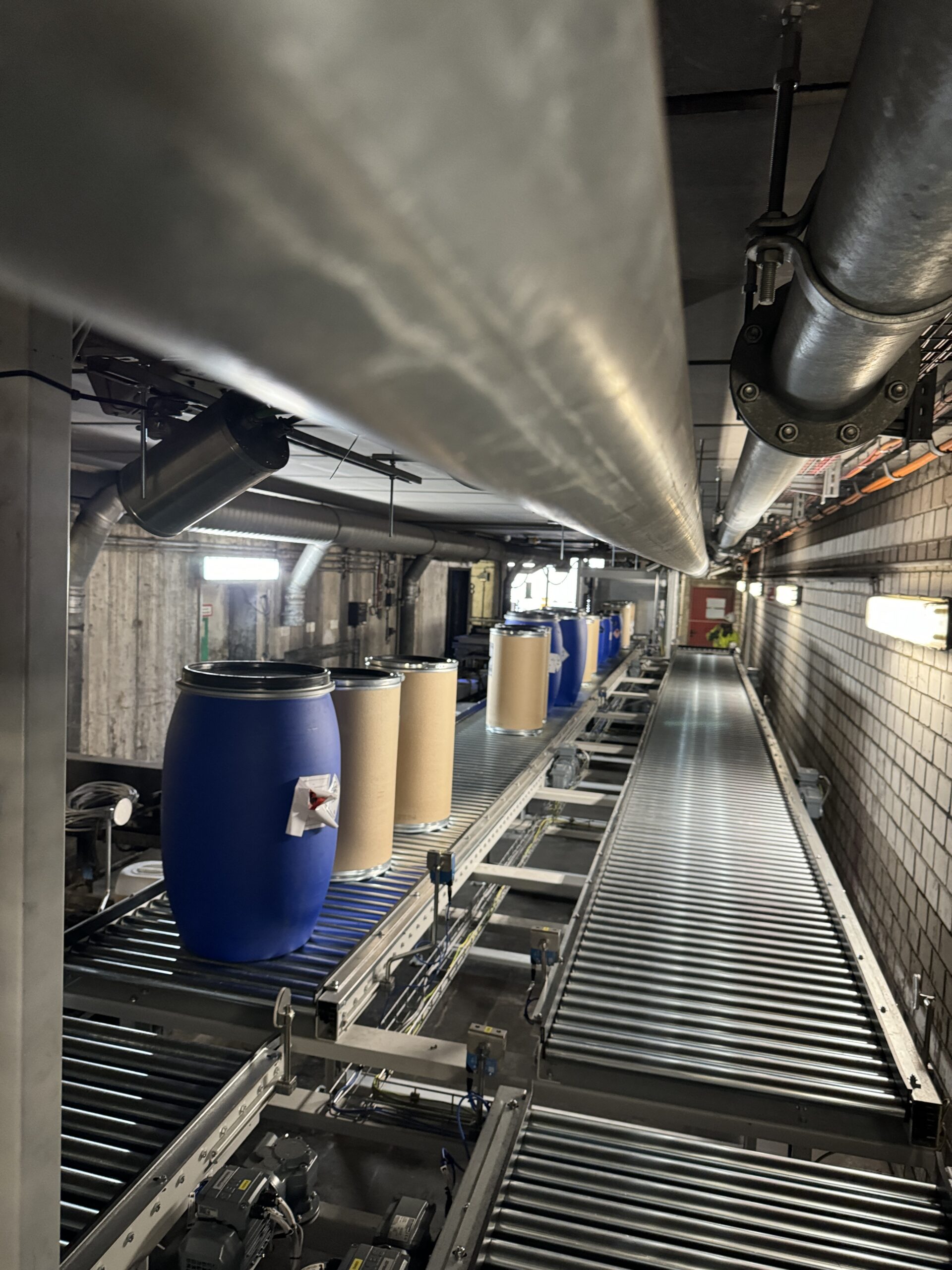
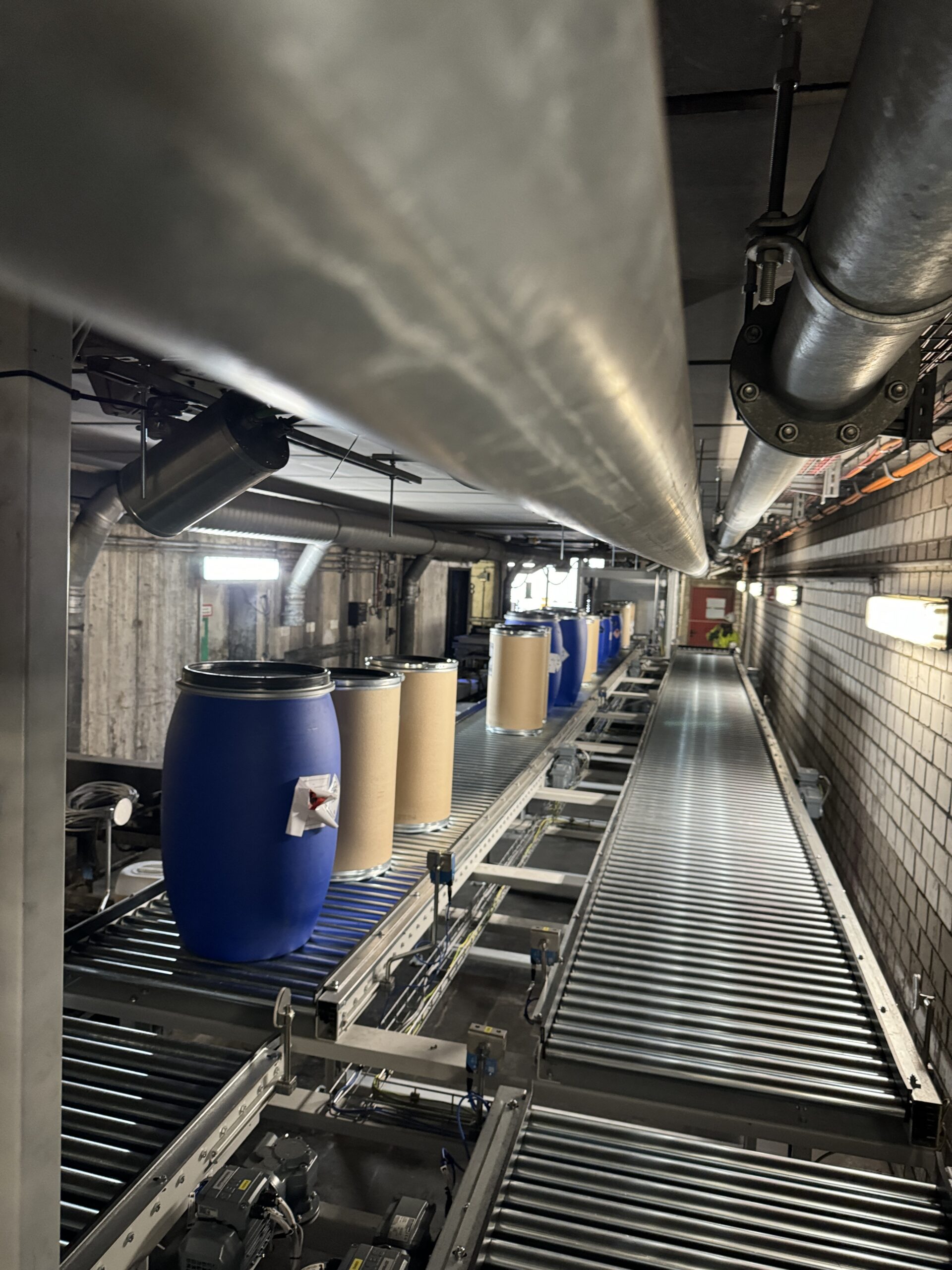
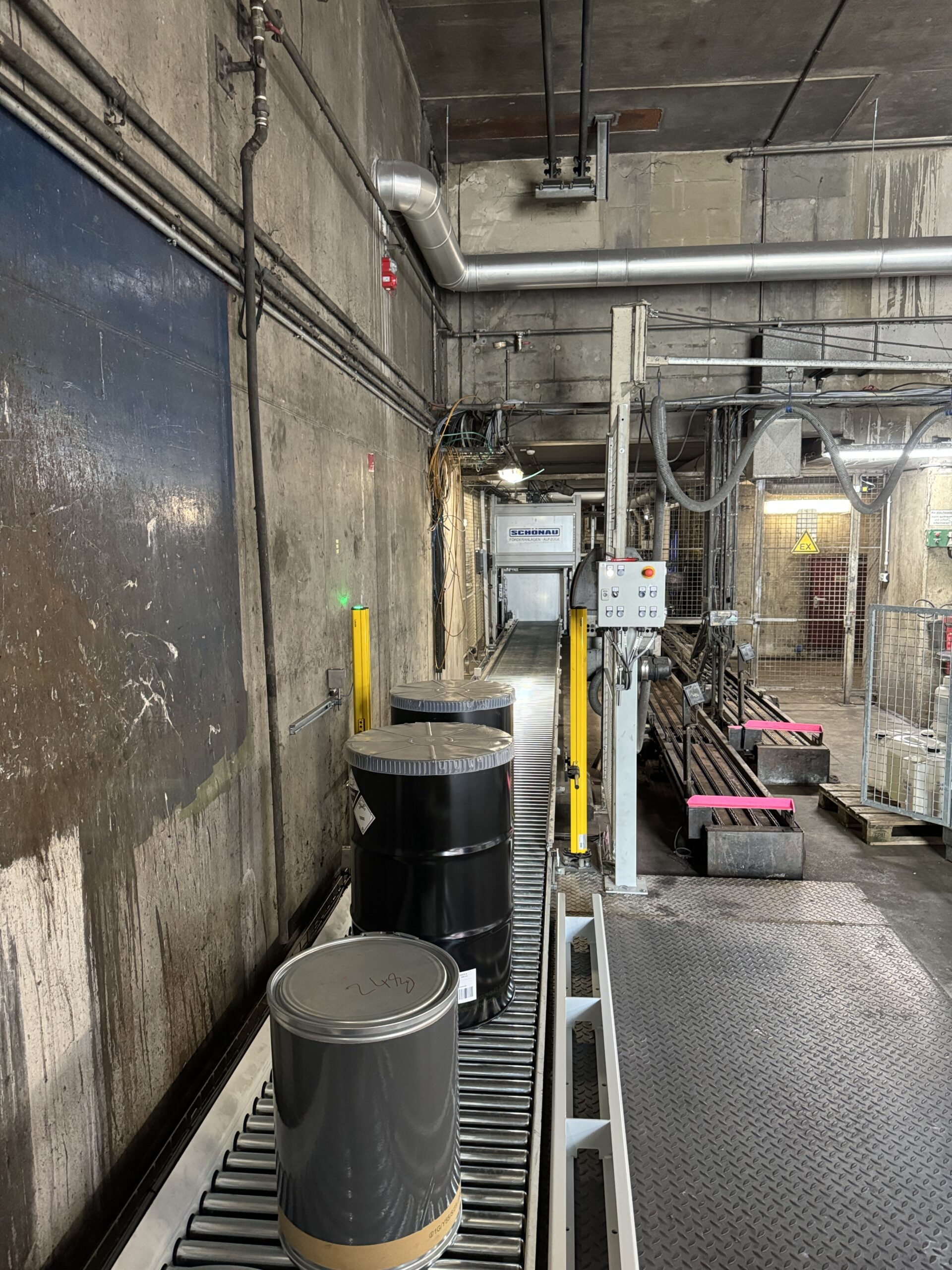
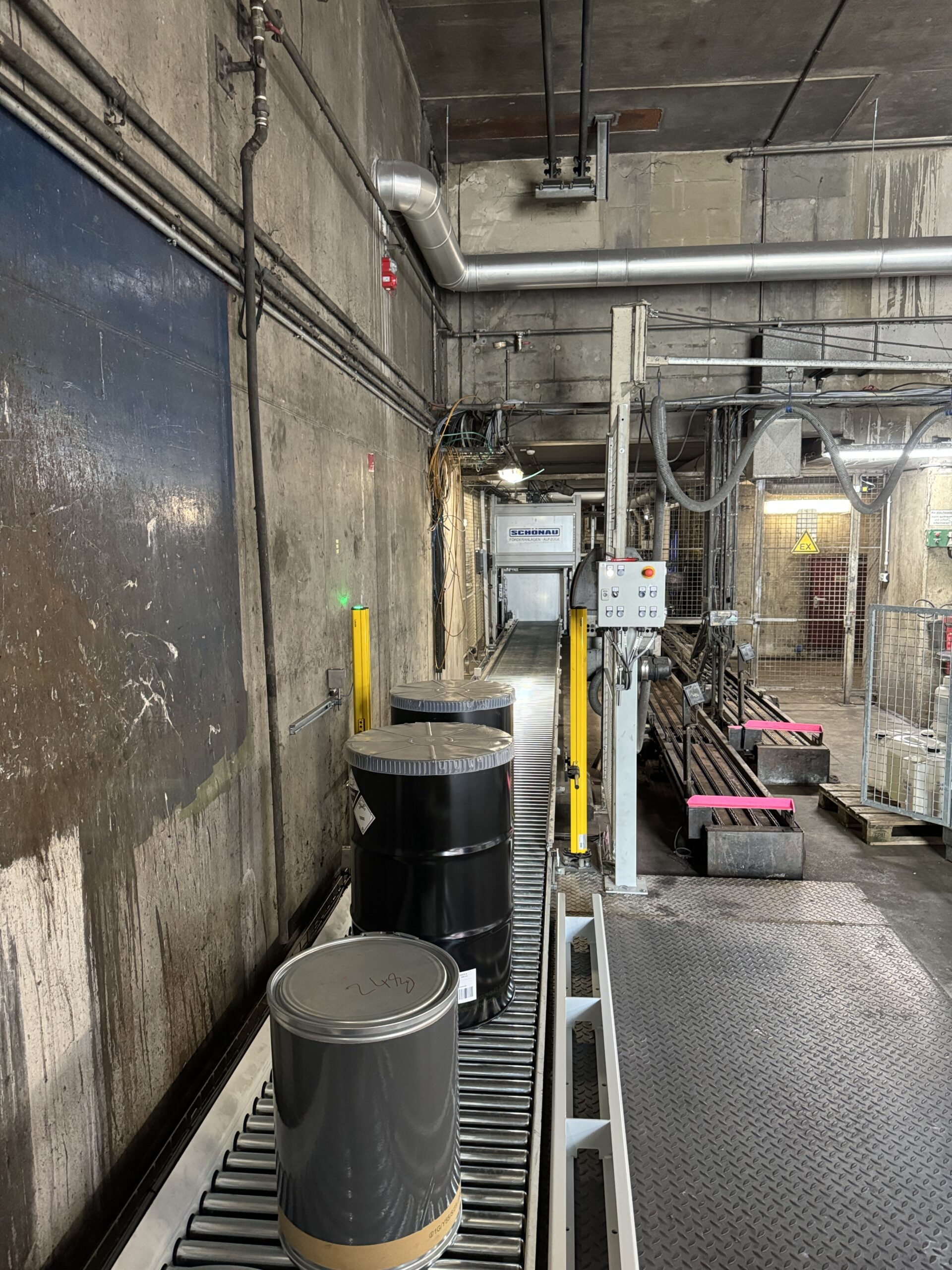
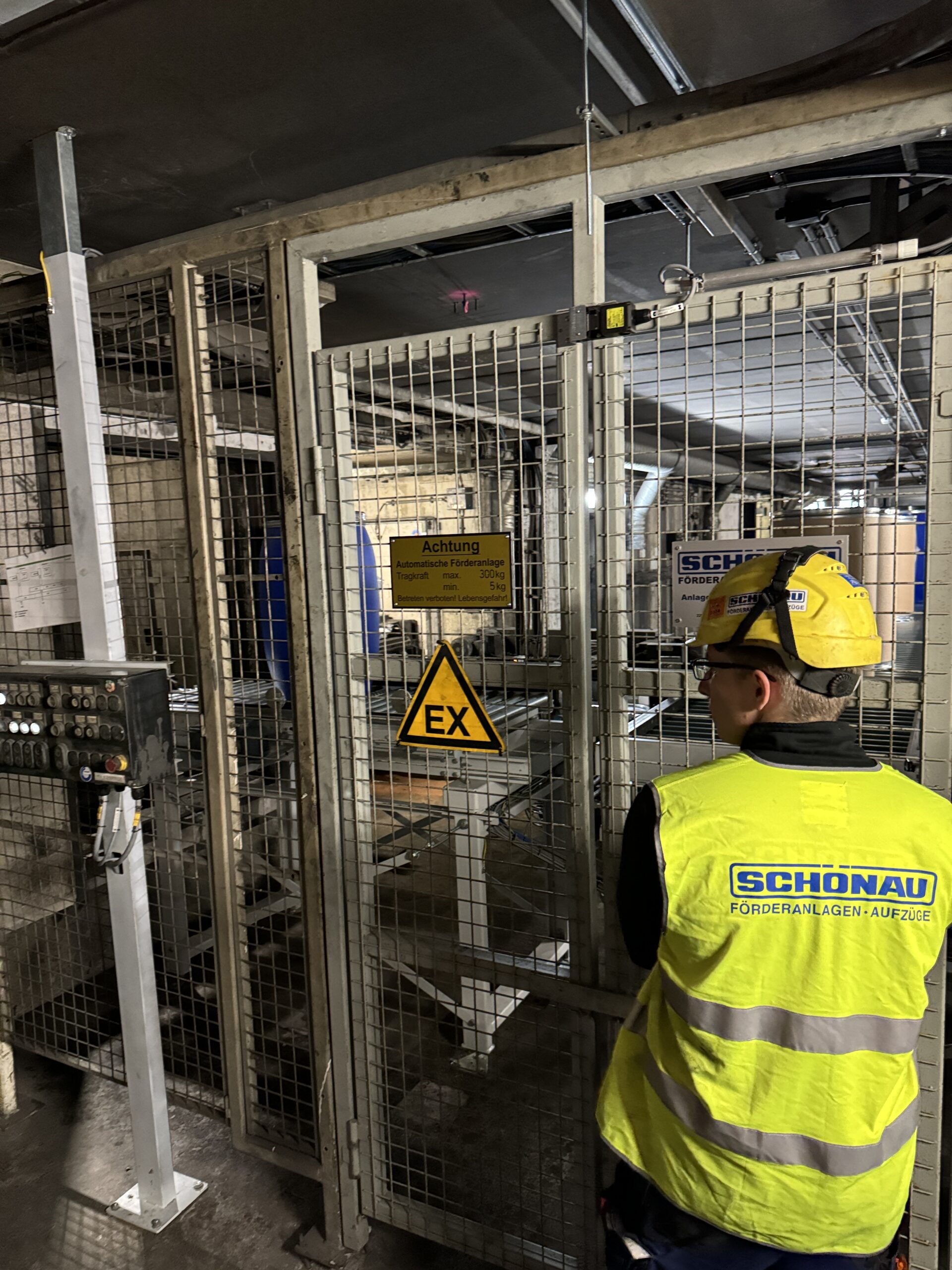
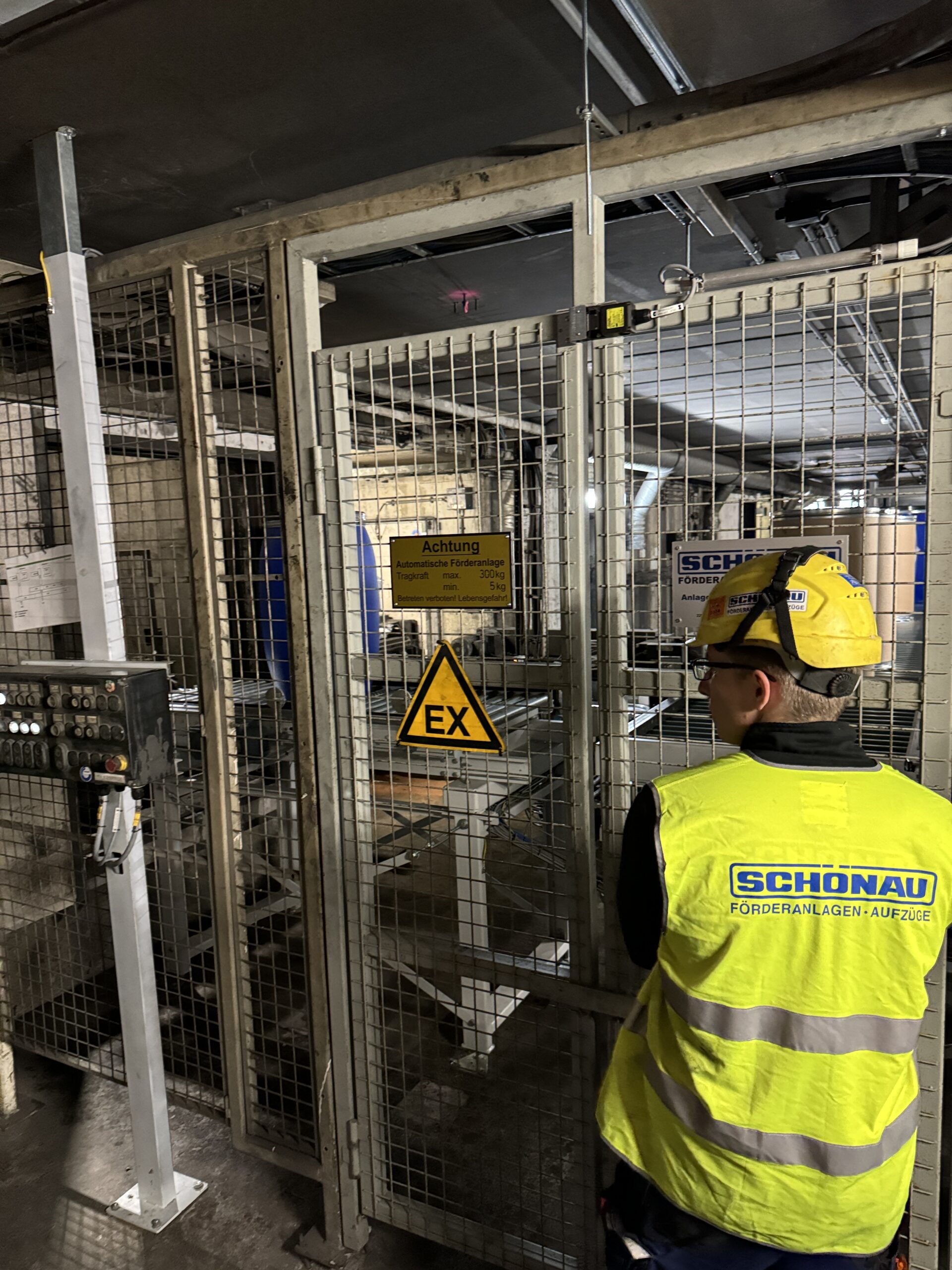
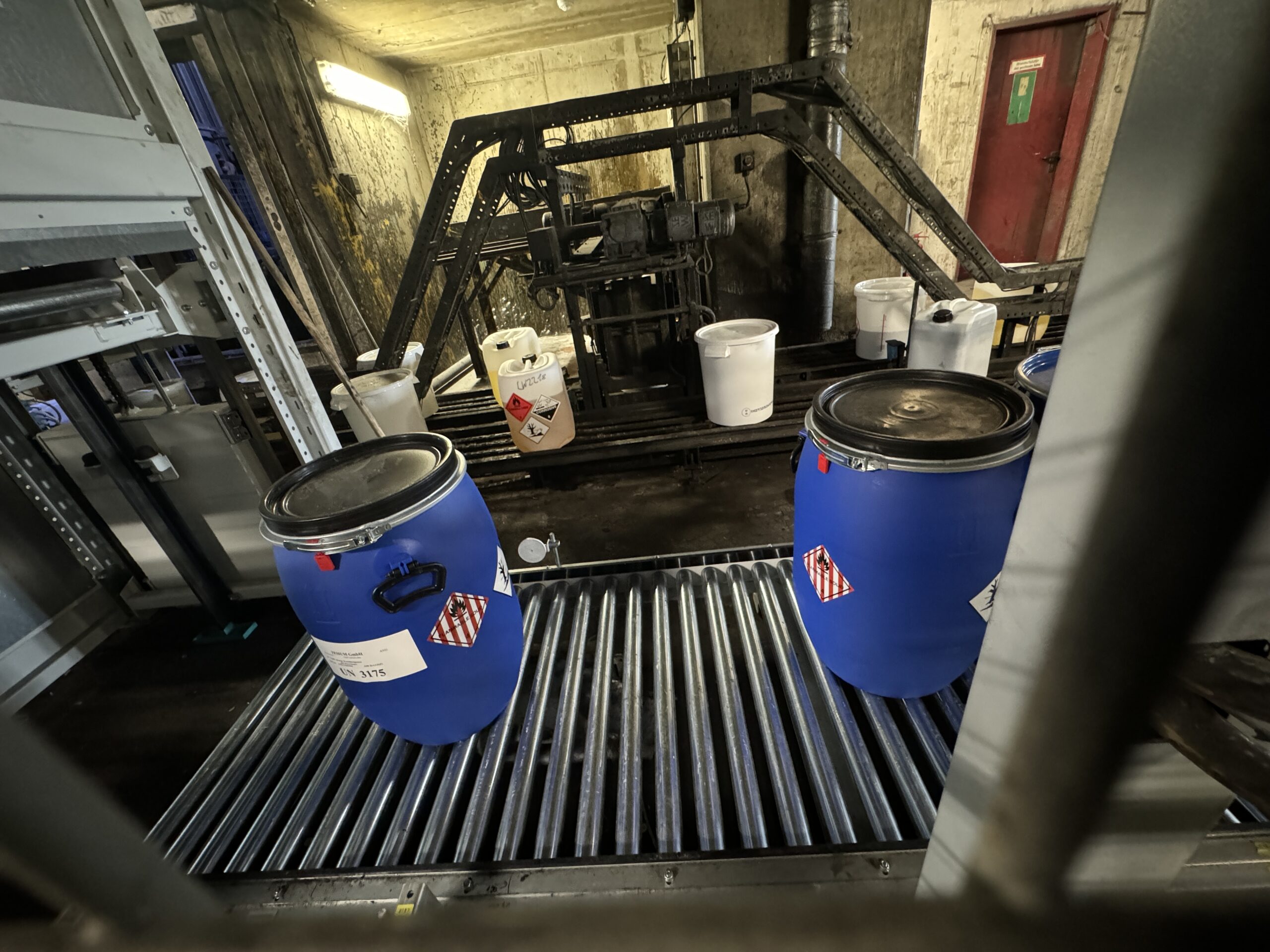
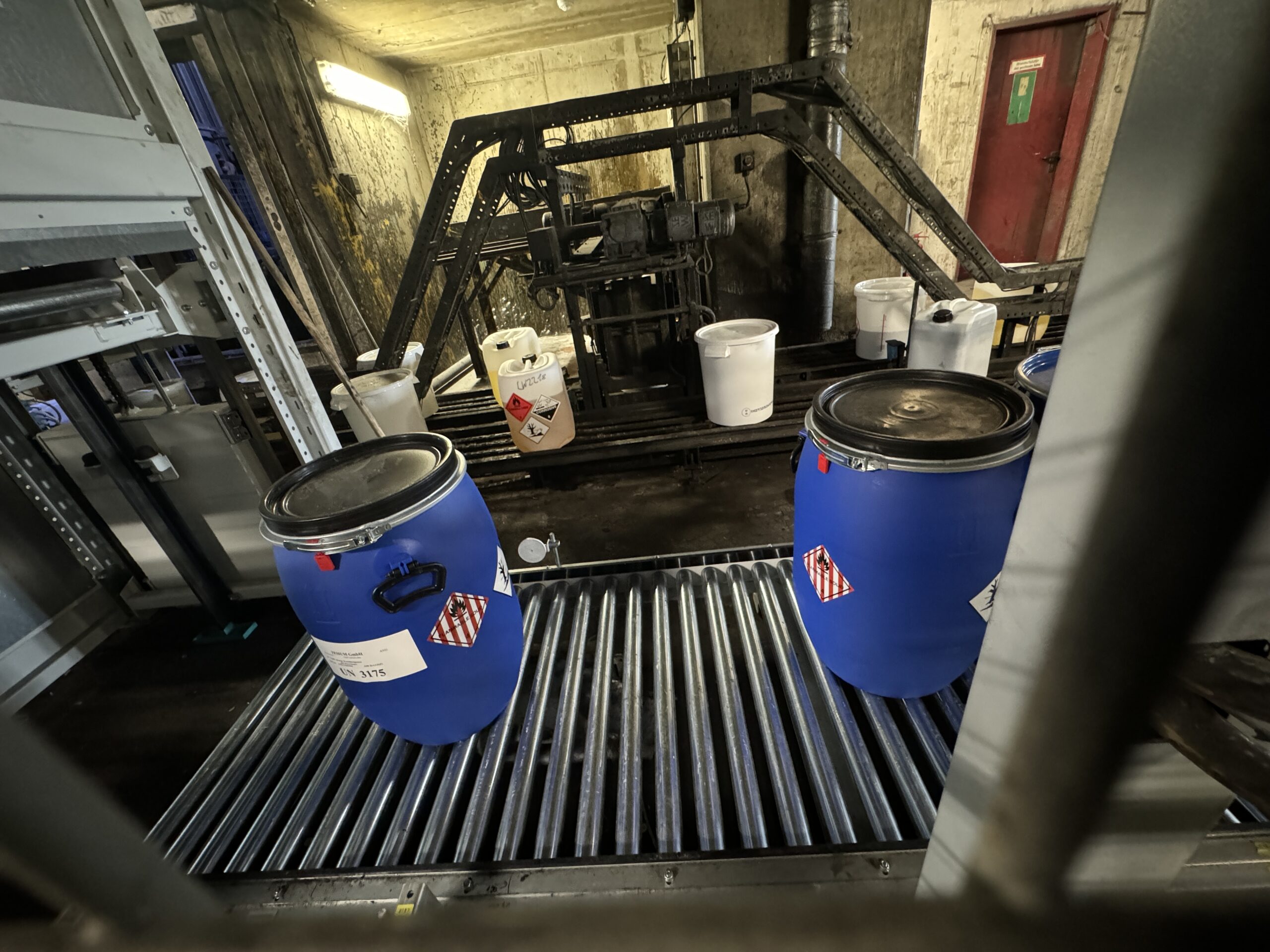
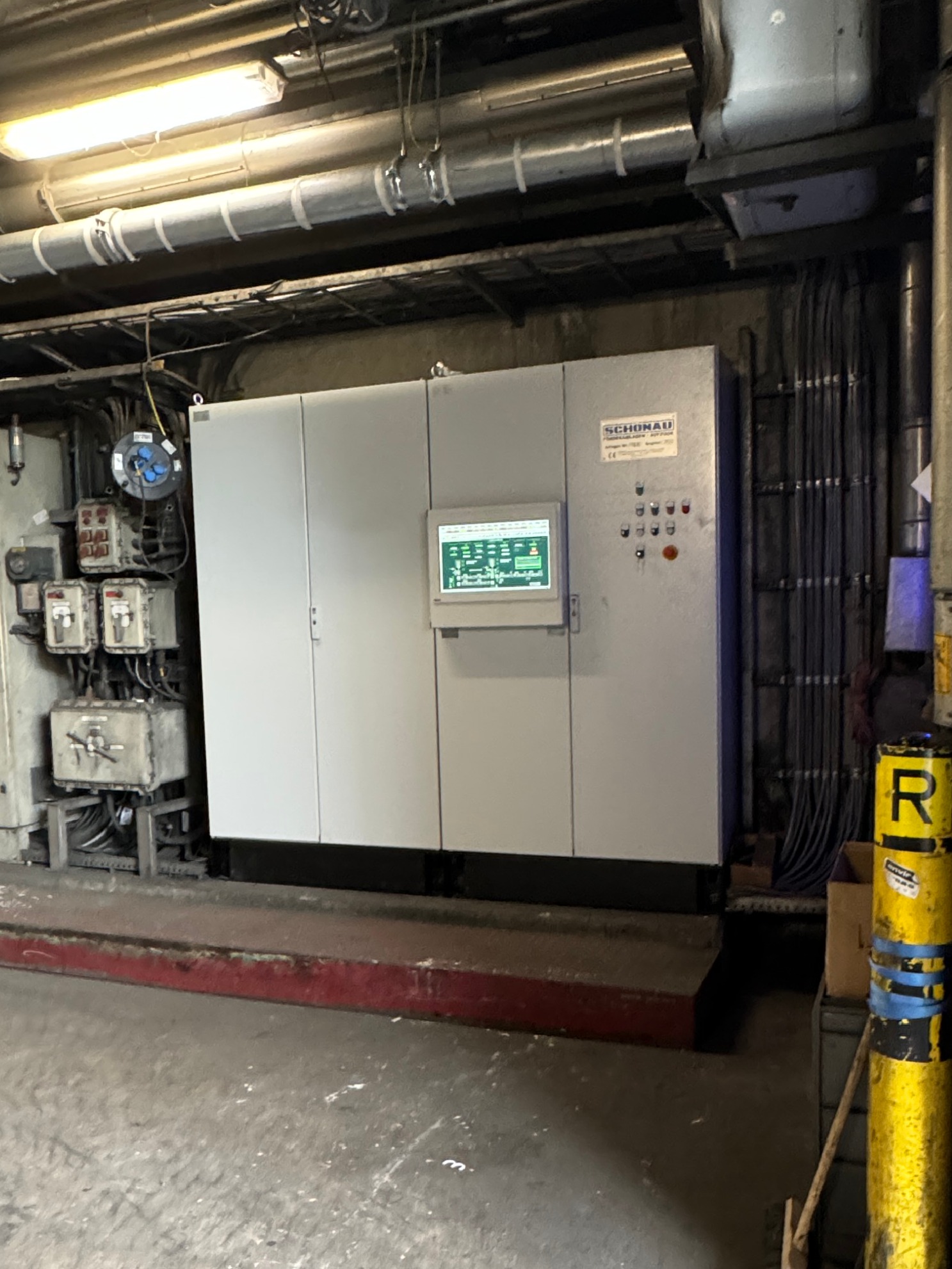
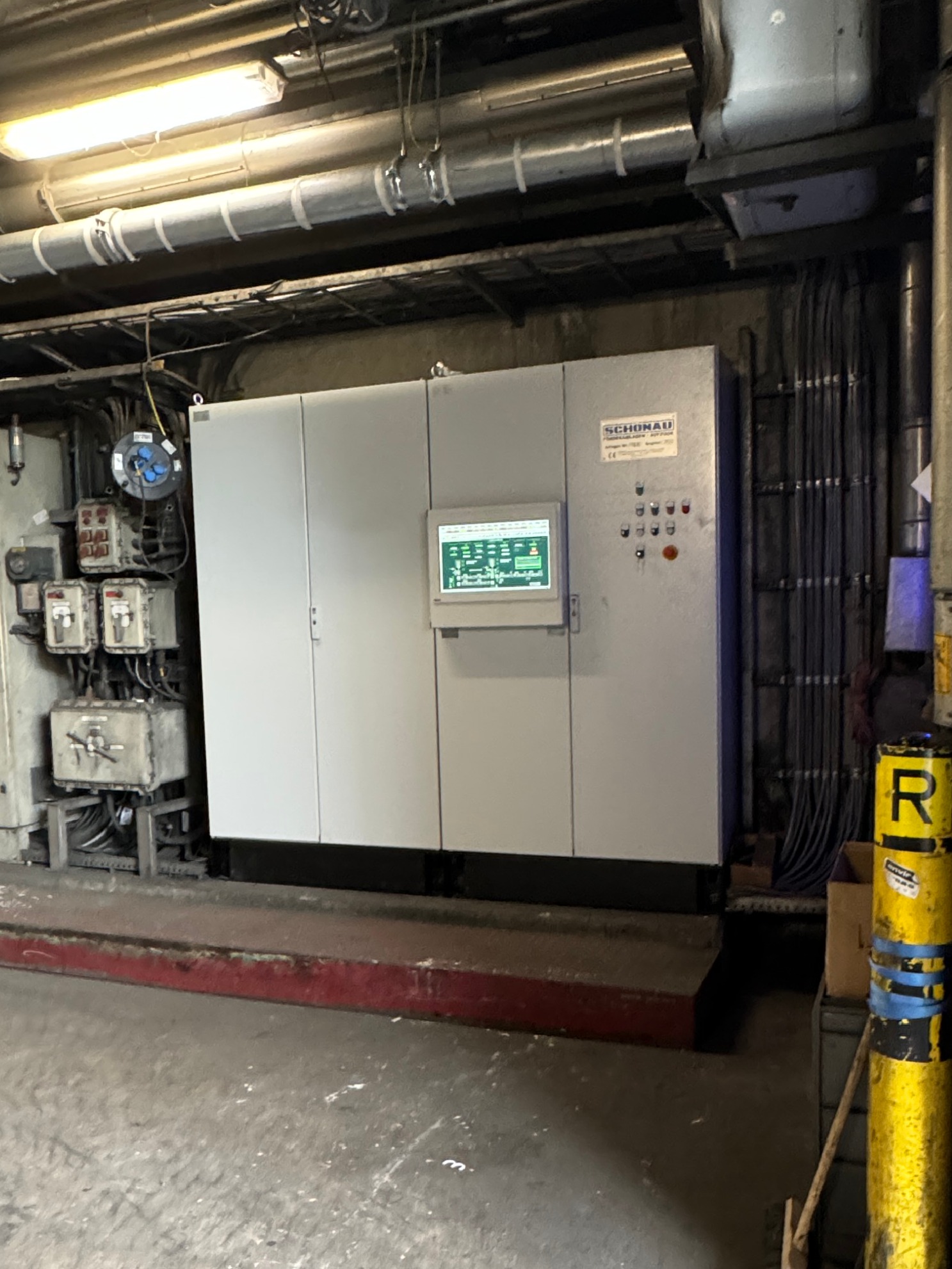